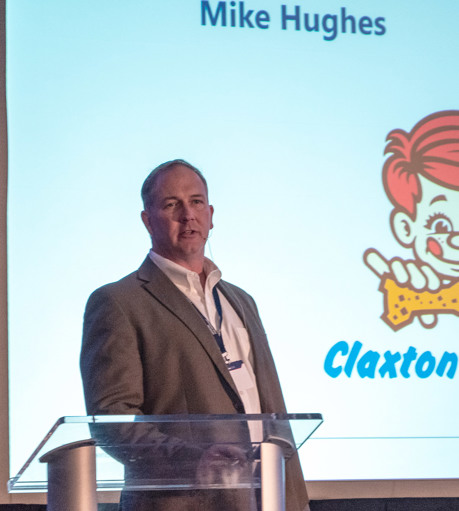
The challenge
Mike Hughes, Debone Plant Manager at Claxton Poultry, presented at the Florida, US, Software KnowHow in 2024. He shared with the audience the significant operational challenges that were affecting Claxton’s bottom line and how Marel Software and hardware helped the company get back on top of excessive trim and waste levels. As well as improving all-round operational efficiency to regain their customers' confidence.
With weekly production of over 9 million pounds (4 million kilograms) of ready-to-cook chicken, even small inefficiencies result in substantial losses. “Our throughput was terrible.” Hughes recalled, “We couldn’t regulate our machines. Our sizes were coming out all over the place and we just couldn’t process it effectively. Along with that, we had trim waste with an excess of 23%. That is just unacceptable, we were throwing millions of dollars down the drain."