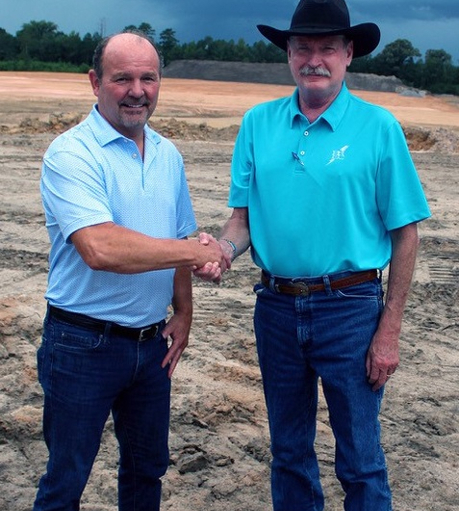
Focus on automation
The USA accounts for almost half of global turkey production. The market is stable, showing some growth. Automation is a high priority for turkey processors striving to increase yields, be more efficient and less dependent on labor. It is therefore no wonder that Prestage Farms focused initially on automation for its new greenfield plant. Choosing Marel automated solutions was entirely logical, as experience has shown these to be leaders and the best in their class in the turkey industry.
From the labor-saving perspective, Prestage Farms only needs about 300 people to run its new 100 tpm [6,000 tph] turkey plant. This number is relatively low, because the company's end products are mostly bulk turkey cuts, not needing any manual further processing or packing operations.
Picture: Larry Campbell (Marel VP Sales Poultry USA) and Ron Prestage (President of Prestage Farms South Carolina)