Marel can offer several ways of batching legs into fixed weight packs. These use the MultiHead Weigher, a Marel grader or Robobatcher. A fourth method, which too often goes unnoticed, is overhead leg batching. This is, in fact, an easy method, as it uses components available in an ACM-NT line and keeps products in the shackle.
Combining chicken legs inline to make up A-grade trays
Fixed-weight overhead leg batching
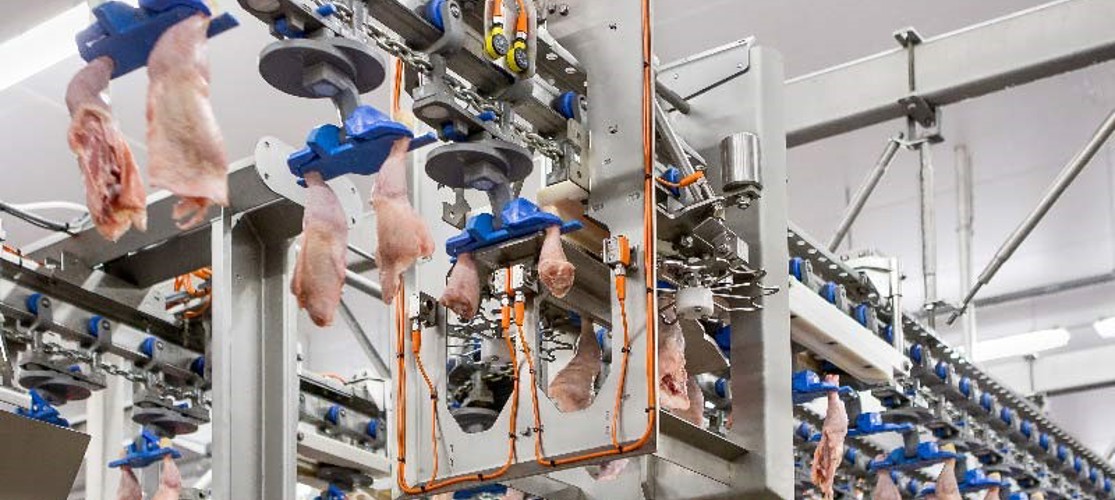
A most practical way of creating fixed-weight batches of whole legs is by making use of the Overhead Leg Batching configuration, consisting of ACM-NT modules, Leg Weigher, Broken Leg Detector, Leg unloading stations, batching hoppers, PaceLine packing line and Innova PDS.
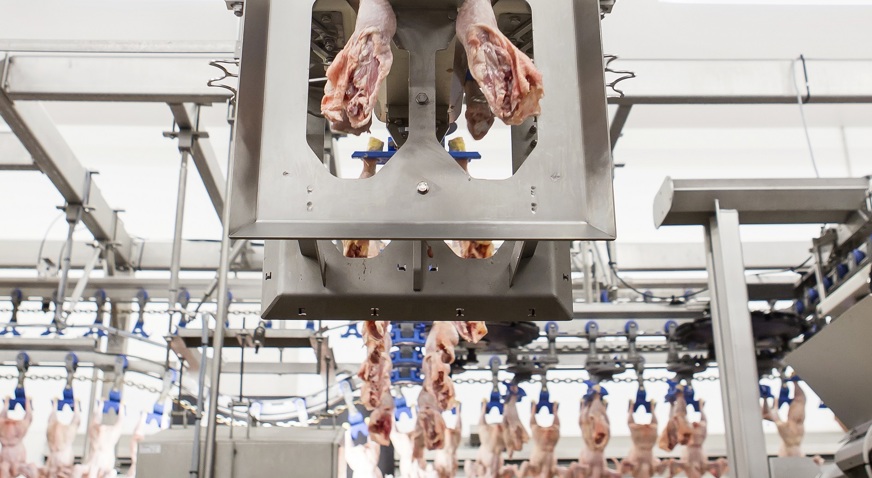
Buffer line
An IRIS system, installed upstream, will already have checked the leg quality of all products visually. After legs have been cut off in the ACM-NT line, they pass the Leg Weigher. This weighing module takes each leg out of the line to weigh it individually and hangs it back automatically afterwards.
The Leg Weigher transfers weight information on each leg currently in the line to the Innova PDS software control system, which will also have gathered data on its quality from IRIS. Thanks to a smart algorithm, Innova PDS is now able to put together A-grade legs to make up a fixed weight tray of say 1,100 g. These legs have now become a virtual batch. Innova PDS needs some 100 products to be able to make perfect batches of products with minimum give-away. A buffer line must, therefore, be set up to give the required quantity of products to choose from.
Broken leg detector
Installed immediately behind the Leg Weigher in the ACM-NT line, the Broken Leg Detector checks all passing legs for fractures. When a leg is broken, it will not be rigid enough to push the detection wheel outwards. This is picked up by a Broken Leg Detector connected directly to the Innova PDS control system. The leg is then recoded as being broken and will be released at a different destination. For legs not needed for the batching process, the ACM-NT line offers the option of a bulk unloading station, which batches bulk quantities of legs.
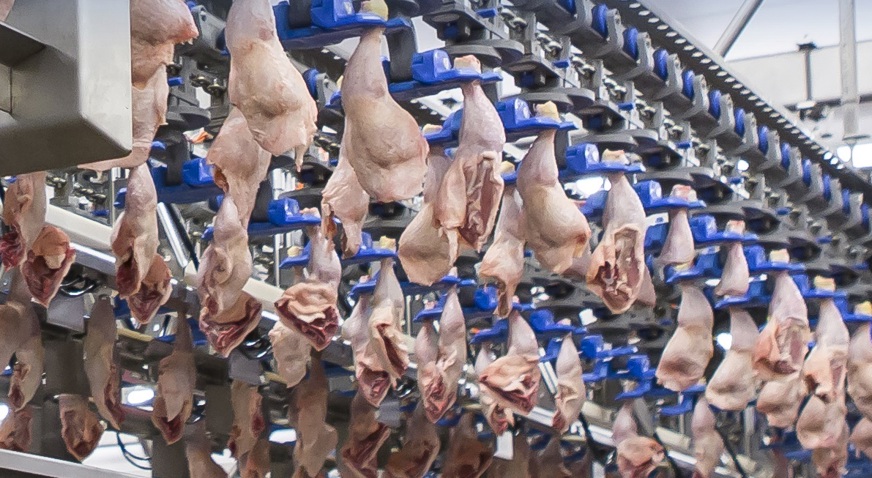
Combining three lines
To be able to choose from even more products when composing batches and further reduce give-away, it is possible to set up two or even three parallel ACM-NT buffer lines. Innova PDS sees these quite simply as one extended line. The ability to combine legs from all ACM buffers, also known as Combined Rate Limiting, makes the exact matching of different leg weights even easier for Innova PDS. It now has 300 products to choose from instead of 100.
Release
The virtual batch of legs destined for a single fixed weight tray and still on the overhead conveyor will be released one by one into the same batching hopper. The number of hoppers needed for dropping batches depends on the customer’s needs and can be configured to any amount.
When a hopper has gathered all the products needed to make up a single fixed-weight batch, it is ready to release its contents onto a conveyor belt. The hopper flap closes and just as soon as a free slot on the belt conveyor comes along, products are unloaded onto it and conveyed to the packing stations.
PacePack
The PacePack packing line has been designed specifically for the manual packing of fixed weight batches onto trays. The belt conveying product batches from the bins is joined by a tray belt running alongside. Trays are fed onto the idle end of the tray conveyor, which can also be equipped with an integral denester. Both conveyors run synchronized. Batches of product and trays run side by side at the same speed.
Operators work together to fill the trays. The first operator places some legs from the batch onto a tray on the parallel tray conveyor. The second operator adds further legs from the batch whilst the last operator completes the tray with any legs still remaining from the batch. PacePack offers the advantage of a constant working pace for all operators, resulting in consistently high output.
Get in touch
Our dedicated team is here to help and answer any questions you may have. Please complete the form, and we’ll get back to you as soon as possible. We look forward to hearing from you.