When opting for a greenfield, this will require more paperwork and incur additional costs. Land will have to be bought and licenses obtained. It will also take longer to realize, typically at least twice as long as an upgrade. If a processor wants to increase volumes and, for whatever reason, an existing plant cannot be extended, the answer is obvious; build a greenfield. The cost of the Marel equipment to fit the new factory out will be between 10% and 15% of the total.
Update or greenfield
How to extend a growing poultry processing plant?
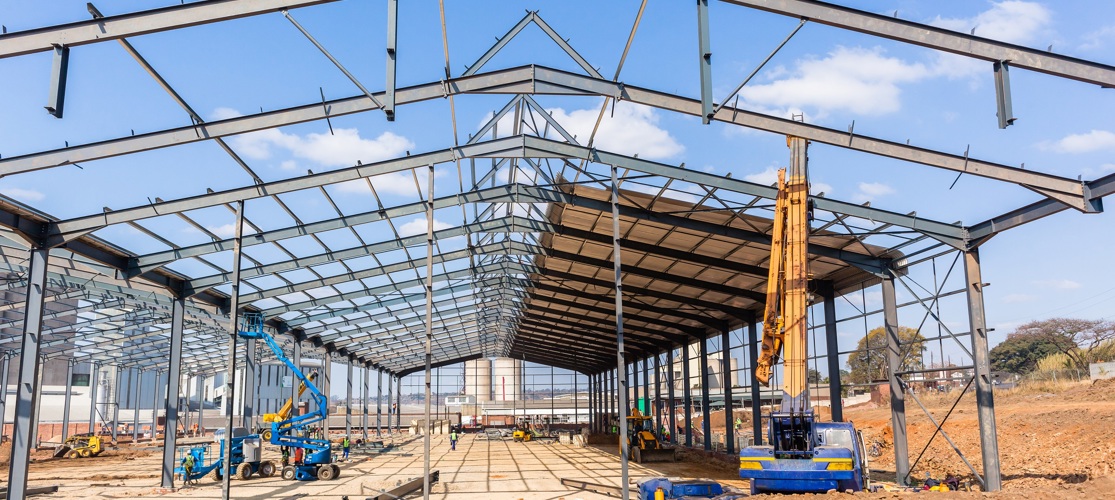
Unlike in developed markets such as North America, Europe and Oceania, markets in the global South have the potential to grow rapidly. This is particularly true of South-East Asia, where the question of extending an existing operation or building a new greenfield plant will arise most often.
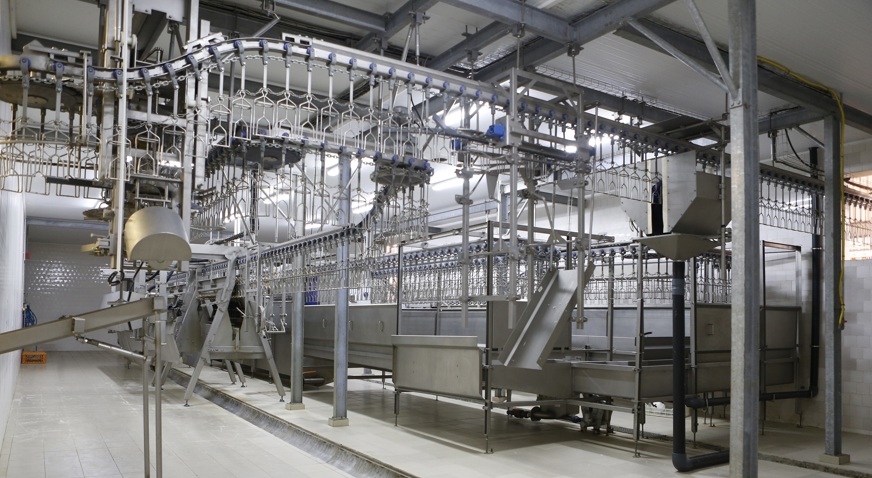
An update is quicker
The answer, however, will often be to update. This is particularly true if the necessary footprint can be accommodated in the existing building and equipment can be installed without impinging on normal production. A good example here is a processor who already has a supply agreement with a QSR chain but who wants to cut costs by installing some automation. His priority is clear; the job should be done as quickly as possible.
What to do when demand increases?
Often, however, the answer is not so clear cut. Many plants will have been built with graded frozen whole birds as their main end product and with little spare space for any secondary process. Only downgraded products would have been cut up. In the meantime, volumes handled by the plant will certainly have gone up and the market could well have changed. Once a market becomes more sophisticated, demand for cut product increases. With the increasing costs and scarcity of labor, the automation of some secondary processes then becomes an issue.
Can the necessary equipment fit into the current building? Can the installation of automation be done in stages? Marel automatic cut-up and deboning systems are modular and will allow this. If there is insufficient space for a fully automatic solution, a mix of labor and machines is also possible, although this should always be seen as a compromise and not a long-term solution.
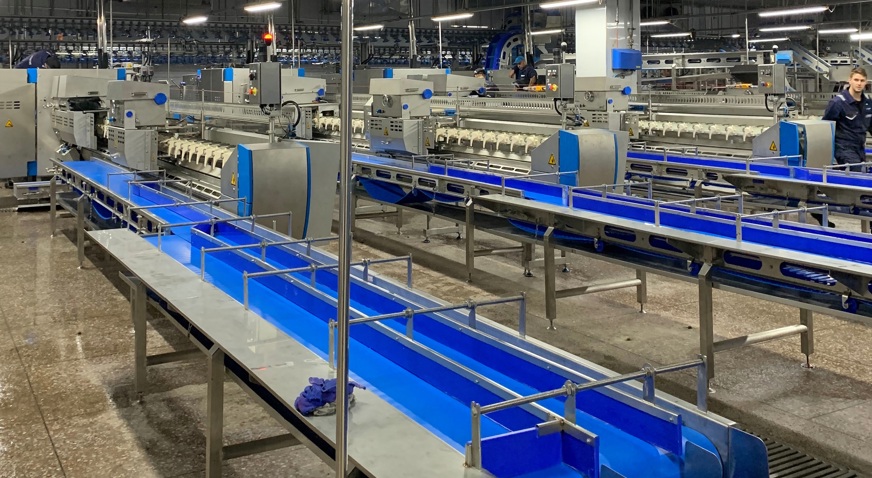
Adding further processing
If a processor is looking to add a further processing line, there is a good chance that there is no space available to accommodate it. Keeping the process entirely separate from the main factory could then be an option. In this case, the efficient supply of raw material to the dedicated further processing operation would also be a priority.
Questions to be asked
When in doubt, further in-depth discussion will show the way forward. Questions to be asked are as follows.
- What are the constraints of the existing operation?
- Which market is the processor aiming for?
- What are the volumes to be produced?
- When should the revamped factory be up and running?
- How much does the processor want to invest and when?
Processors should, however, never lose sight of the big picture. While footprints are important, things can always change. Going too early into too much detail should therefore be avoided.
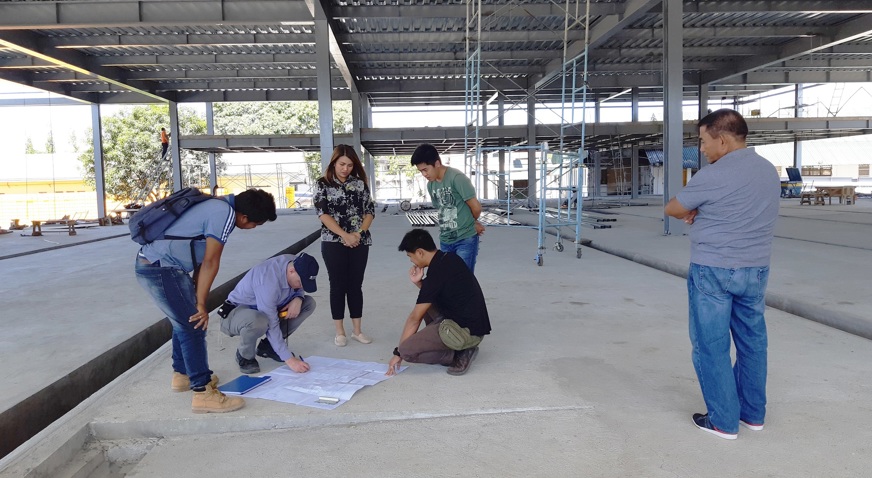
Primary process
As far as the primary process is concerned, there are three situations, which will influence the decision whether to update a processing plant or build new. Volumes go up, the move starts to air-chilled fresh product and volumes or labor issues make the automation of the evisceration department attractive.
The killing department is perhaps where equipment serves the longest and is replaced the least often. Scalders can always be extended and pluckers added to cater for increased volumes or lower scald temperatures. Whether there is room to do this will largely determine whether the solution will be a greenfield or an update. Provided the chilling method remains the same, an update will probably be preferable. Air chillers, however, take up a lot of space. Changing the chill method will usually tip the scales towards a greenfield.
Automatic evisceration equipment can usually be made to fit in an evisceration room, which was previously manual.
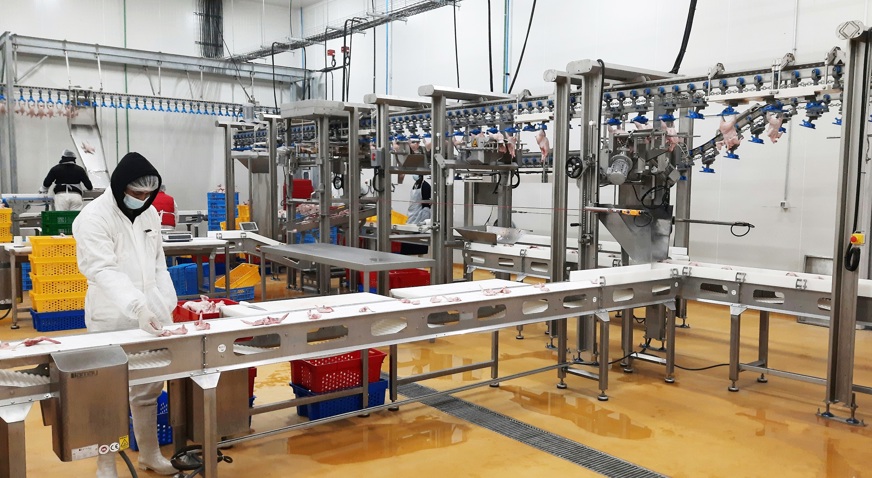
We have omitted the live bird supply department. Many plants, particularly in the Global South, operate a crate-based system. Moving to a containerized system such as GP or ATLAS has many advantages, which include better animal welfare, fewer DOAs and fewer damaged birds. The investment is, however, a large one and will usually only be considered when building new.
Software updates
Adding hardware to update a plant is not the only answer. It is important that the plant has a decent network that responds to the IT/OT requirements to facilitate Marel's software solutions and to prevent unexpected misalignment.
The addition of advanced software can help prolong the life of existing mechanical equipment. Kits are available to upgrade AMF breast cap deboning, FHF front half deboning and SensorX bone detection systems. More data helps process more efficiently.
Most greenfield factories will be built in the Global South, whereas updates will be much more common in mature markets, where any future growth will be slower. Markets in the Global South have ample room to grow and the space to accommodate new greenfield factories.
News
Get in touch
Our dedicated team is here to help and answer any questions you may have. Please complete the form, and we’ll get back to you as soon as possible. We look forward to hearing from you.