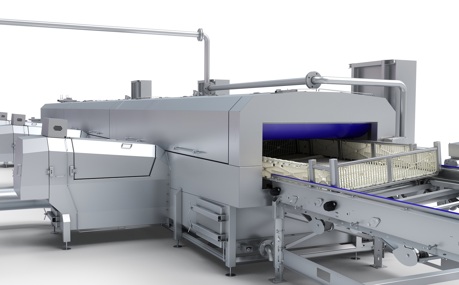
1. SmartStack – cleaner with less
Among the Marel priorities when designing the SmartStack transport modules of the ATLAS live bird handling system, were that it should be easy to clean thoroughly, that the system developed to clean it should use water effectively.
The module, which consists of a variable number of self-nesting trays, has no frame to wash. The trays themselves have no blind spots, while the automatic washing system boasts clever nozzle design and positioning, ensuring extremely economical water use.
Marel has substantially reduced the risk of cross-contamination between flocks and has done this sustainably.