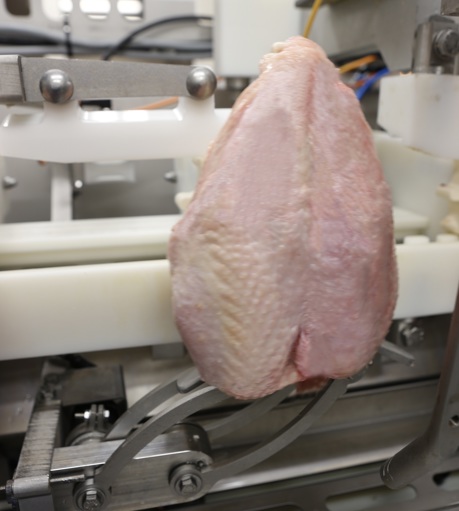
1. Adaptive filleting
Formerly, deboning breasts mechanically was fine, provided the mechanical system used was fed with uniform breast caps. If not, yield and product quality would suffer. Processors often avoided this problem by grading breast caps beforehand, a time-consuming exercise, which often caused production planners headaches.
With the introduction of its AMF-i modular breast cap filleting system, Marel has solved this issue. The solution is known as “adaptive filleting”. Immediately after breast caps have been loaded on their carriers, an intelligent measuring unit checks each one. The unit then signals all downstream modules to set themselves automatically to process the breast cap just measured. Irrespective what size a breast cap is, AMF-i will handle them all, even if a small breast cap is followed by large one, which is again followed by a small one. Yields will be optimum in every case. The production planner’s life will be a lot easier. He will have much more flexibility in meeting incoming customer orders.