Five ways in which Marel can help processors save energy now follow. These are in process order.
5 ways in which Marel helps you save energy
How to make poultry processing more sustainable?
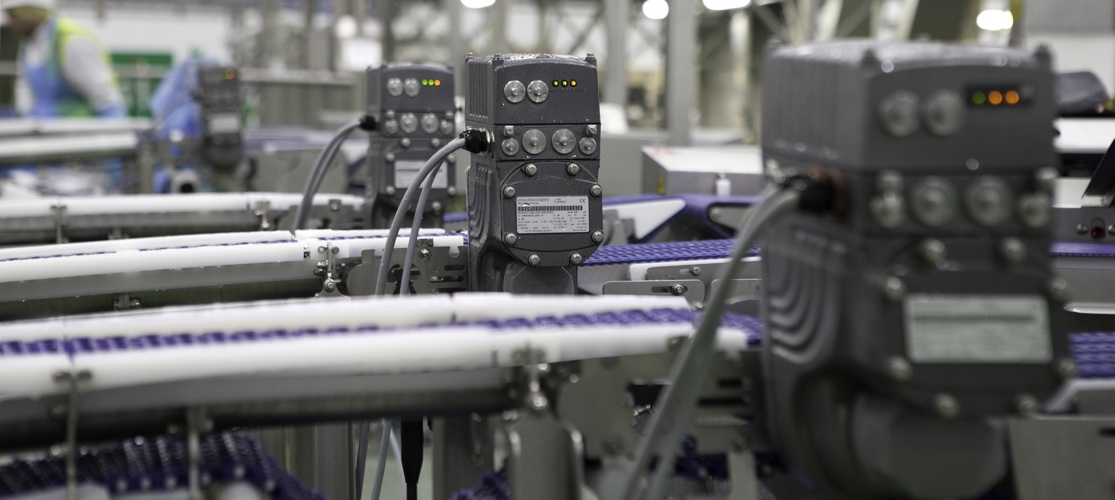
These days, saving energy is about much more than optimizing a processing plant’s bottom line. It is also about saving our planet from the potentially catastrophic effects of global warming. It is Marel’s sincere commitment to developing still further the long-term sustainability of food processing. Therefore, the company is continuously on the lookout for reducing the amount of energy needed in the food process. In the specific poultry process, there’s still room for improvement.
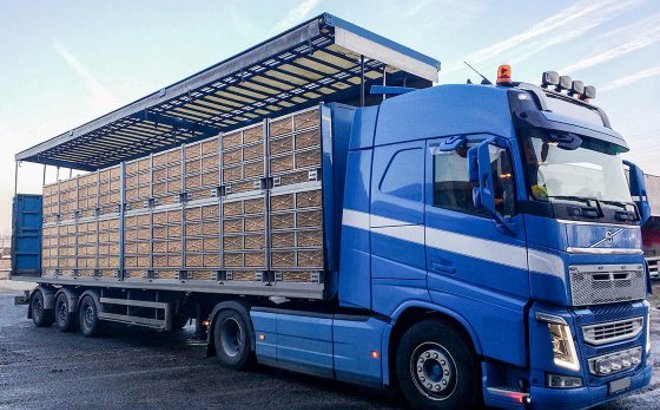
1. Save fuel
For Marel, processing broilers begins when they are ready to be collected from the farm. Using trucks to transport them to the processing plant, however, involves the burning of fossil fuels, heavily implicated in manmade global warming. Reducing the amount of fuel burned by reducing the necessary number of journeys between processing plant and growing farm is therefore a highly desirable goal.
This was one of a number of factors influencing the design of the ATLAS transport module. The module’s innovative pallet doubles as an extra tier, enabling the accommodation of up to 38% more broilers. Trucks can therefore accommodate more birds, resulting in fewer trips and less fuel burned.
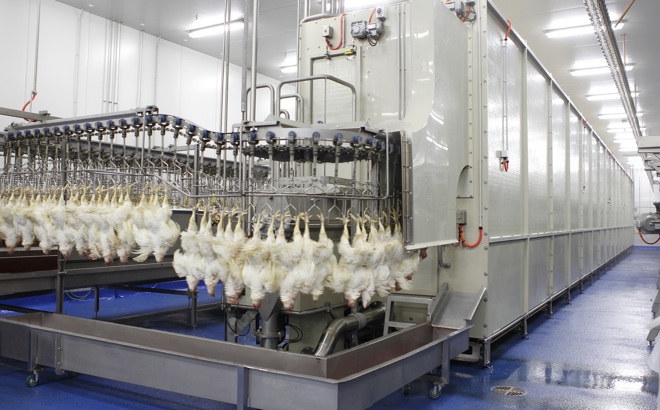
2. Cut scald energy use
Scalding is another significant user of energy. Water in the scalding system has to be heated up and kept at a given temperature. Heating is by direct steam injection or, more usually, indirectly by hot water recirculated through radiators in the scalder itself.
There is an energy-saving alternative. Marel’s AeroScalder uses moisturized hot air to scald broilers. The system blows the air forcefully over the carcass, after which it is reconditioned for re-use. Compared to conventional scalding, AeroScalder can cut energy usage by up to 50%.
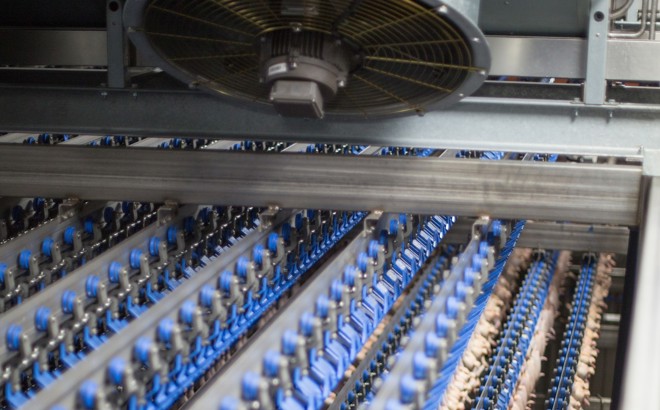
3. Chill energy-efficiently
Air chilling is the most energy-intensive step in the poultry process. To optimize shelf life by counteracting temperature pick-up during cutting, deboning and packaging, many processors now strive to chill carcasses to a core temperature that is as close to freezing point as possible. This is a big challenge, as there can be no freezing of thin extremities such as wings and neck flaps. The laws of physics dictate that removing more heat will require more energy. Getting calculations right on critical aspects such as fan speed and anticipated chiller loadings becomes even more important.
Marel air chilling solutions, based on many years’ experience, aim to balance energy efficiency and footprint in the best way possible without compromising shelf life, yield or quality.
Lower energy inputs and even better product quality are key priorities for research and development at Marel, the ideal being to create the best possible and least energy-intensive chilling environment around each individual carcass.
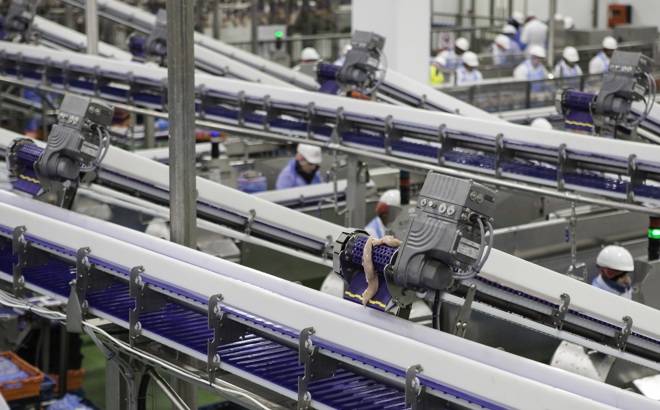
4. Consider energy inputs when moving product around the plant
Moving product around the processing plant is a major energy consumer. In the primary process, this happens on overhead conveyors, in the secondary process on belt conveyors.
Well-thought-out logistics, a top priority for Marel, are the cornerstone of internal transport solutions, which are truly energy-efficient. Product should move smartly through each department, taking as direct a route as possible without obstructing walkways and staff access to processes.
For multiple drive overhead conveyor systems operating at high line speeds, Marel offers its tried and tested ATC automatic tension technology. The system ensures uniform chain tension throughout the line by fine-tuning the speed of each individual drive. Besides prolonging chain life, ATC also helps lines equipped with the technology run at optimal energy efficiency.
In the secondary process, Marel’s SystemFlex modular belt conveyors feature variable speed electric motors operating at constant torque over a very wide range of speeds. It is possible to connect these motors to a central management system, allowing the speeding up or slowing down of individual conveyors in a system. Energy consumption is therefore always perfectly in line with production requirements.
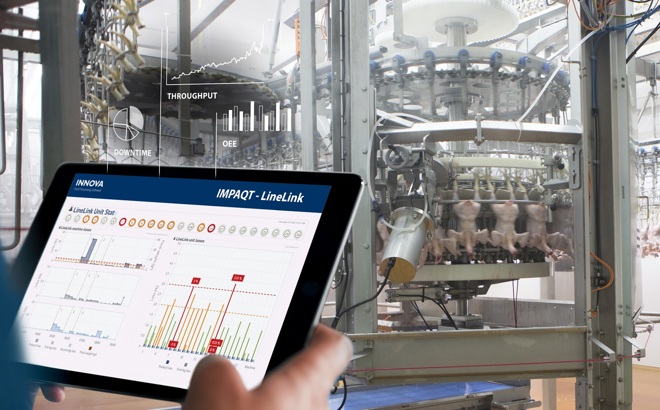
5. Make the most of your process
You don’t know what you don’t know! To manage properly, you need accurate data on a continuous basis. A software platform that understands the poultry business uses that data to create a highly efficient processing line, with the lowest possible energy consumption.
Automated poultry processing consumes energy. Downtime, lines running slower than they should, performance and quality issues all mean that the process is not as efficient as it could and should be. To have complete control over the amount of energy used, plant management must know in as much detail as possible what is actually happening in their primary process on a minute-by-minute basis.
Innova IMPAQT software provides real time information on three critical indicators, availability, performance and quality. If there is an issue with any indicator, IMPAQT immediately identifies the cause, even down to the below par performance of a single eviscerator unit.
Maintenance staff no longer have to spend valuable time tracking down a problem. Concrete up-to-the-minute data replaces gut feel and allows remedial action to be taken immediately, keeping any production losses and energy wastage to an absolute minimum.
News
Get in touch
Our dedicated team is here to help and answer any questions you may have. Please complete the form, and we’ll get back to you as soon as possible. We look forward to hearing from you.