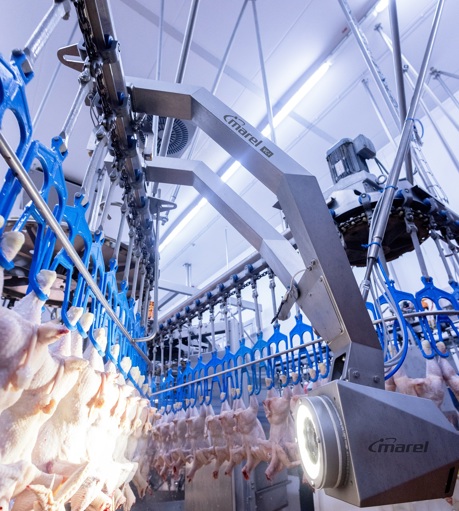
Automated settings
The digital recipes, which take account of the anatomy of a given flock, are responsible for setting the machine. This does away with the need for manual adjustments based on guesswork and reduces the risk of human error when setting the machine. When entering a recipe via the HMI touchscreen, there are four automatic settings. These are:
- Electric height adjustment of the VC-i is set via the HMI screen. The VC-i will adjust its height automatically according to the recipe entered.
- Drilling depth into the carcass can be set by the millimeter, allowing the drill to go precisely as deep as needed without touching the intestines.
- The backplate ensures step-less adjustment of the product relative to the drill. This will depend on the product’s size, type and anatomy. Accuracy of the positioning of the backplate gives much more flexibility than a simple button for small, medium or large flocks.
- When entering the VC-i, an infeed guide directs product into the machine’s units. This requires no more manual settings based on gut feeling.