When increasing automation and deciding where it will make the most difference to your lines, there are three key points to consider.
Three-point approach to transform pork processing into a flexible and efficient solution
Automation in primary processing
With increasing speed, the red meat processing industry is changing their slaughter methods from the conventional manual handling to an automated and robot-driven process.

Setting benchmarks in the meat processing industry
As a full-line supplier, our state-of-the-art meat processing equipment, systems and software span the entire production value chain, from the reception of live animals to the dispatch of finished products.
We work with all processes in the slaughter, cutting and further processing hall as well as case ready and food service packing, all of which can be integrated with Marel Software.
Whatever your location, business size or objectives we can help you to operate at peak productivity and enhance the overall quality and value of meat products
Choose your species:
Marel Food Processing Software
Marel Software enables food processors to collect and utilize data effectively, improving processing results and ensuring full traceability throughout the production process.
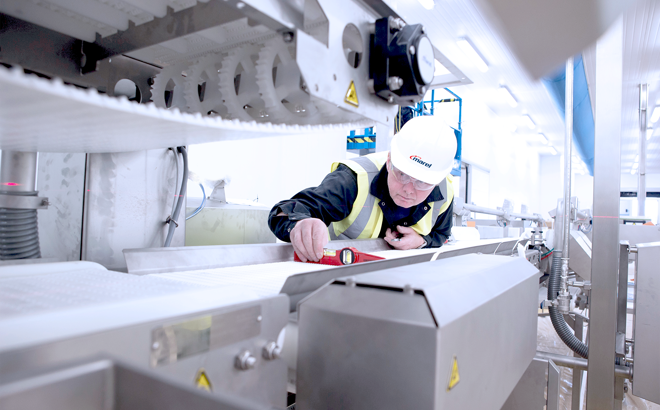
Service
Marel provides remote as well as onsite service support, through customized service agreements. We also supply quality spare parts for our customers, to ensure optimal performance of Marel equipment.
Marel is fully equipped to support our customers all over the world. With offices in 30 countries across all regions, forming a global network of highly skilled professionals, our service partnerships keep production lines optimized and competitive.
Tailored service solutions offer a range of benefits while providing peace of mind that production lines will run smoothly, with minimal downtime and optimal efficiency.
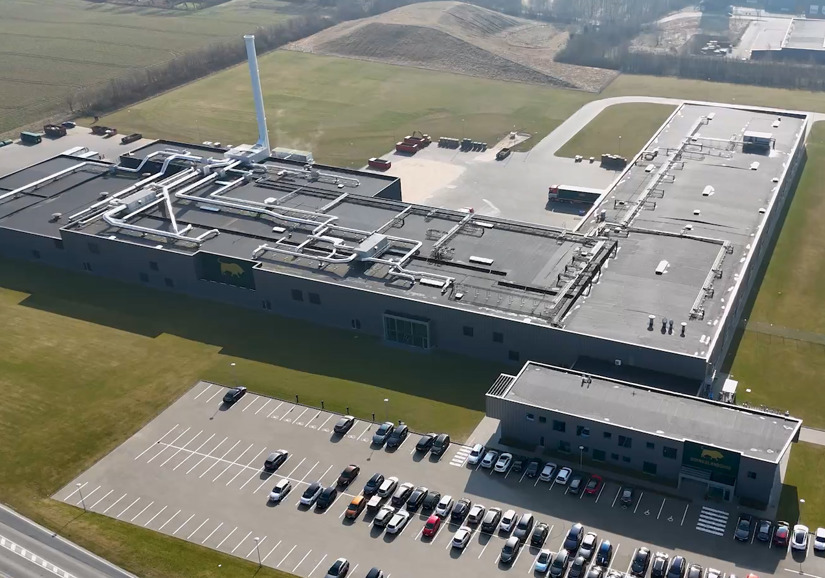
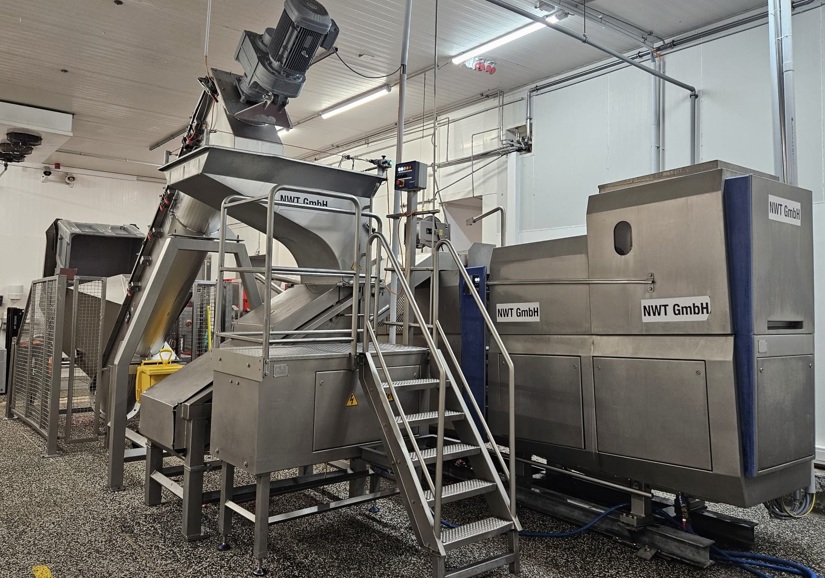
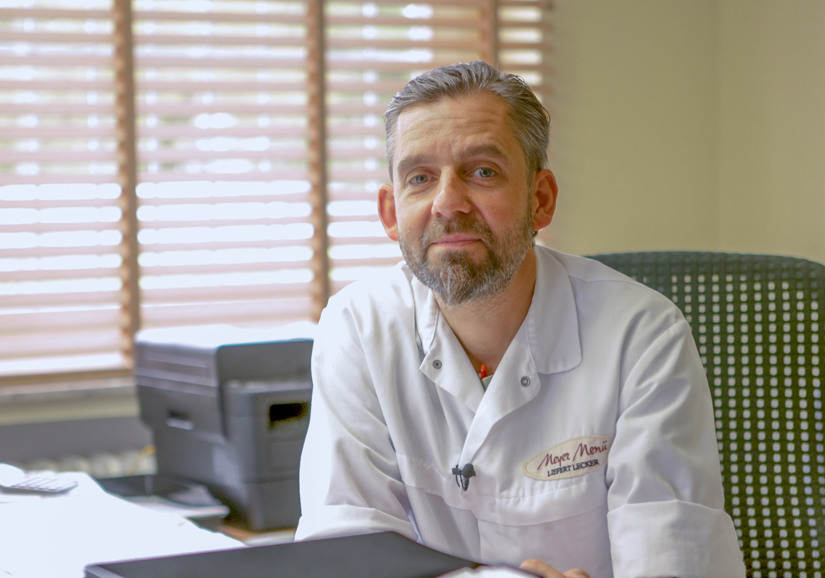
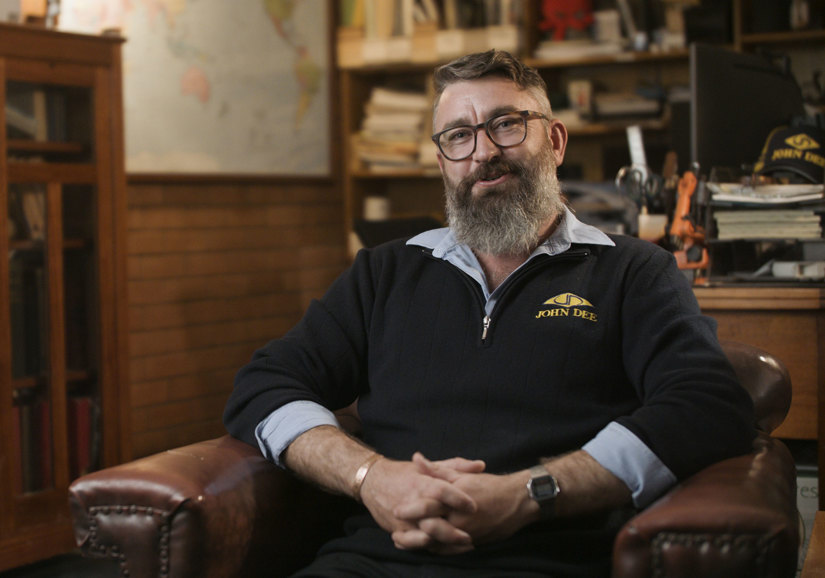
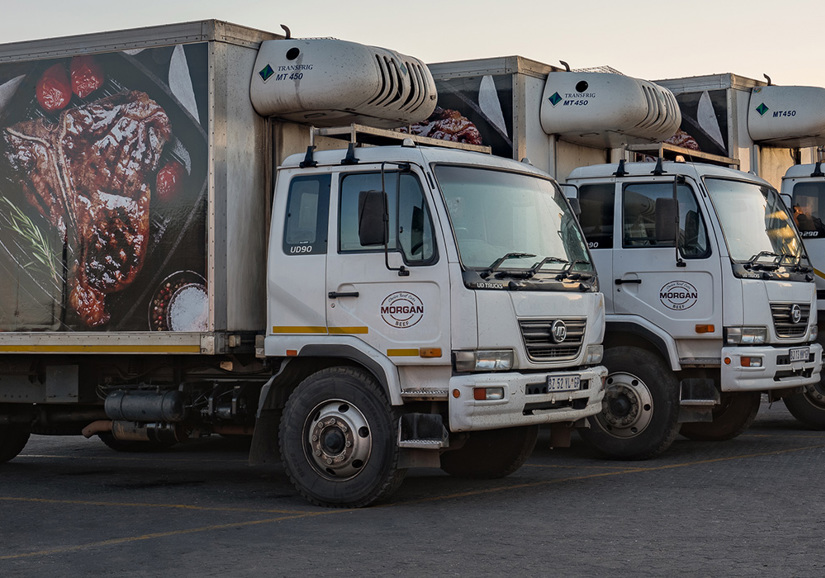
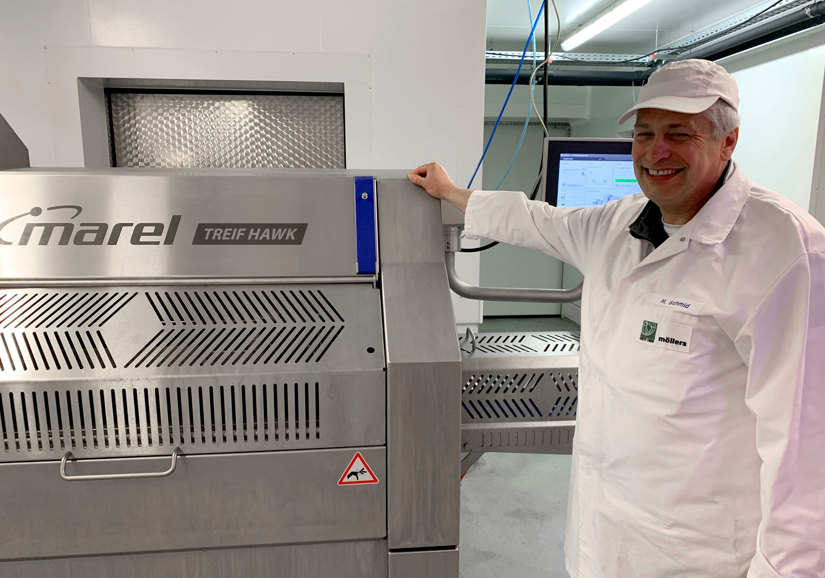
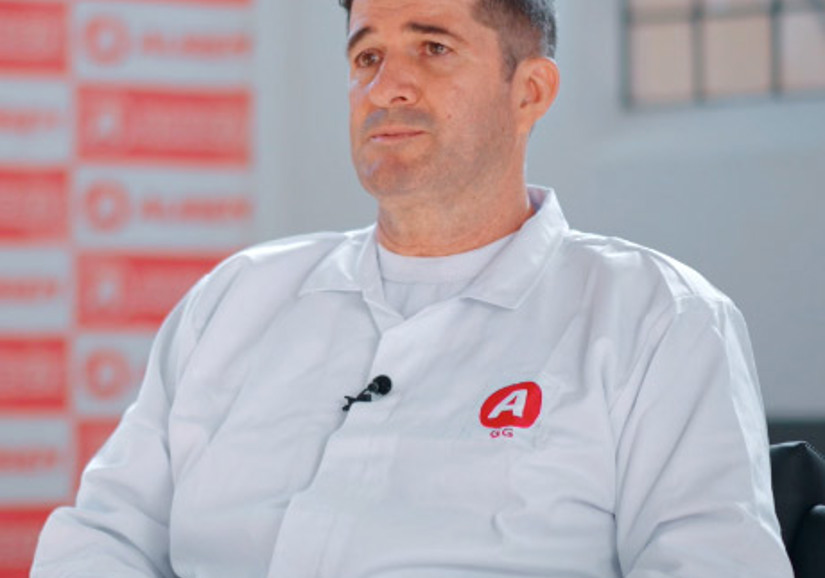
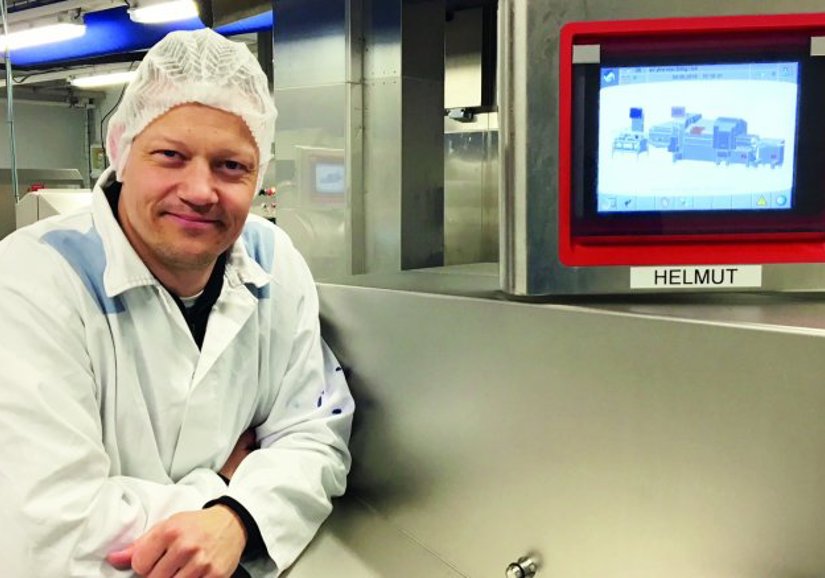
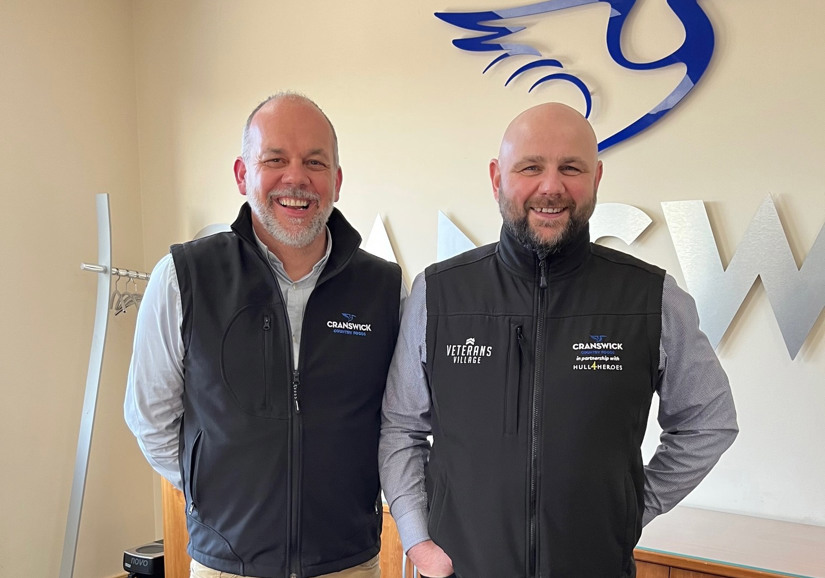

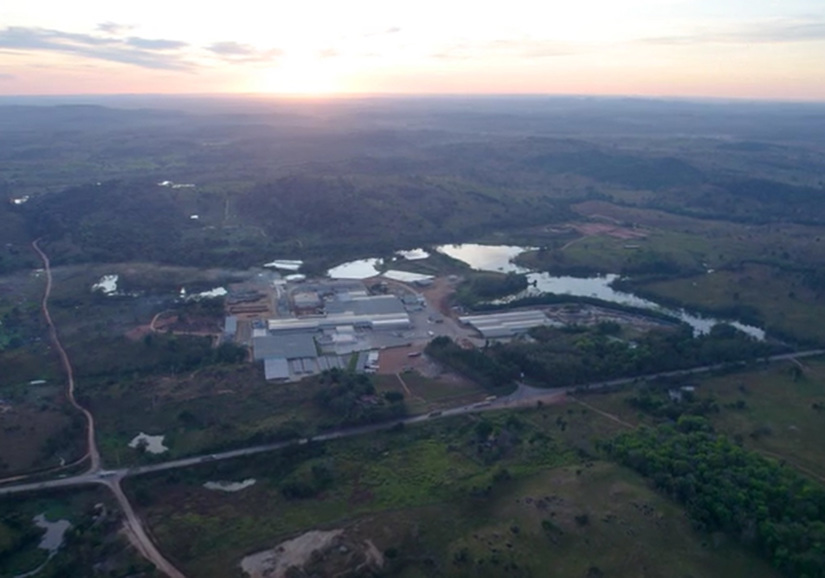

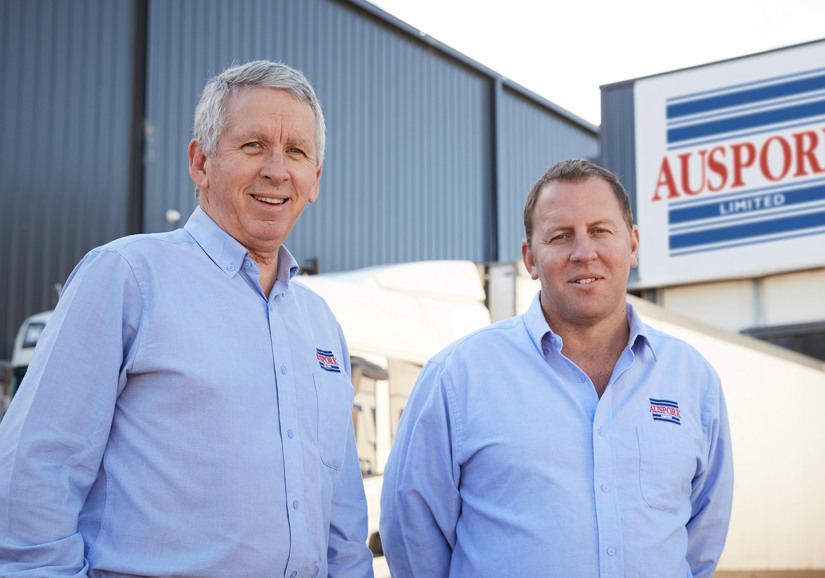
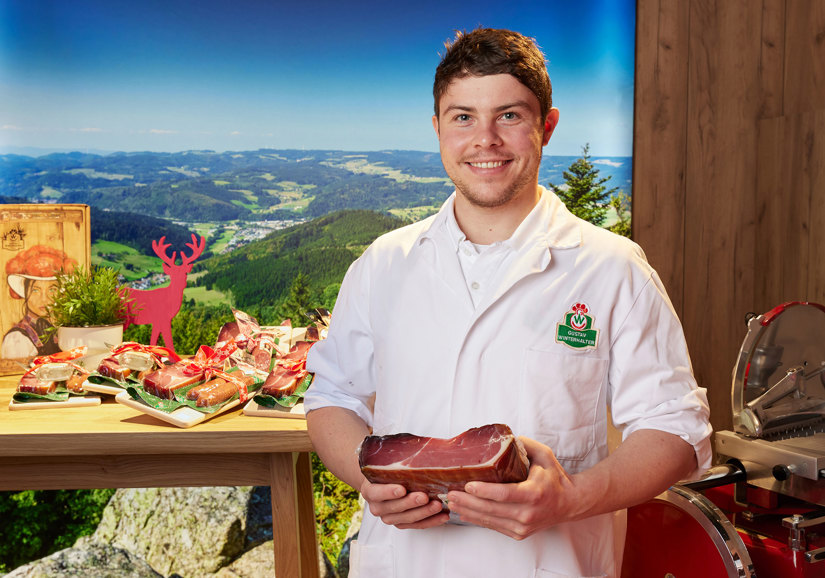
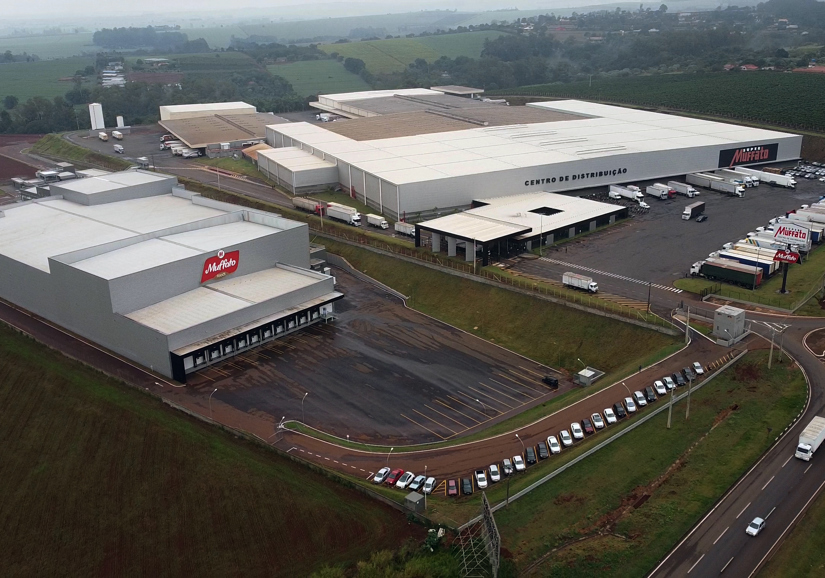
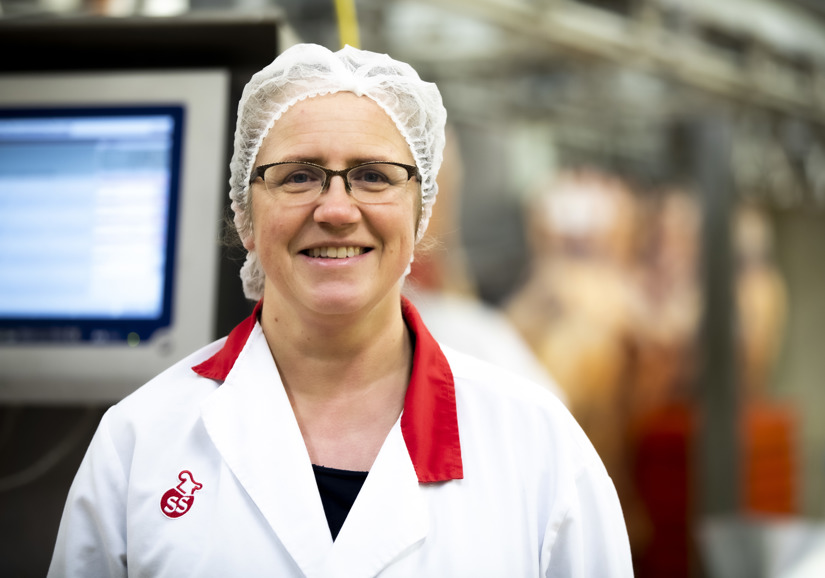
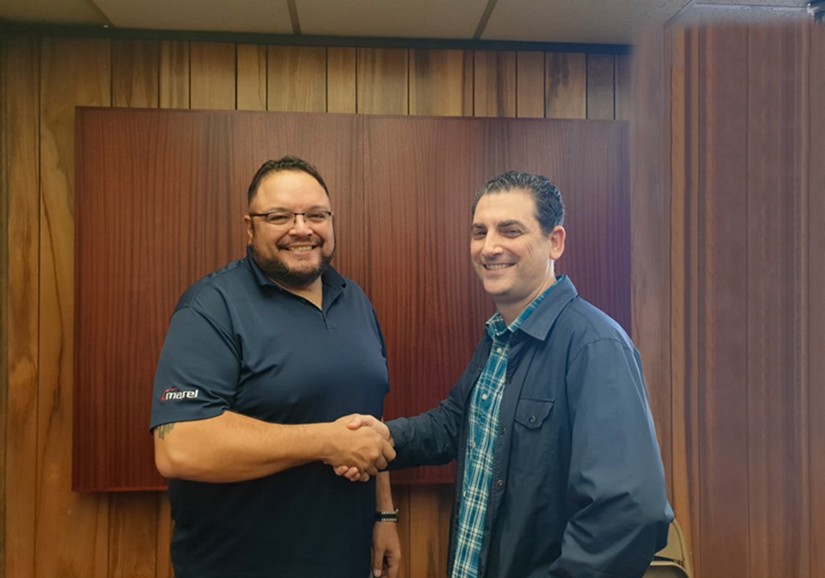
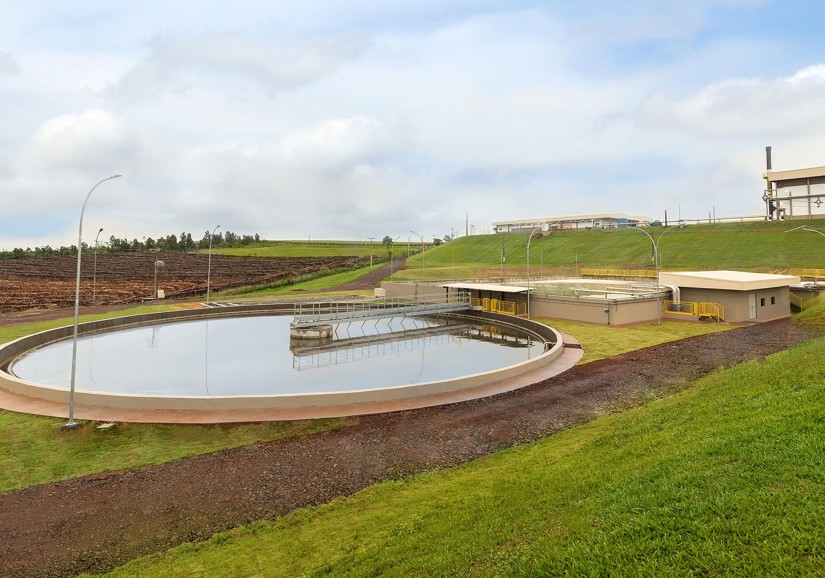
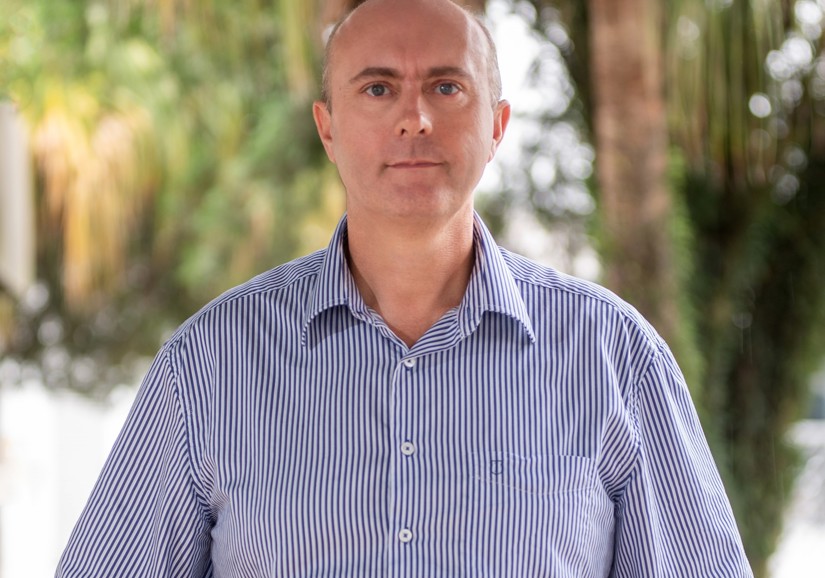