Today, the turkey production volume worldwide is stable and slightly growing. It represents approximately 5% of the total poultry market. The USA accounts for almost 50% of that market.
Just like in the broiler industry, the turkey processing industry shows a high demand for further inline automation, related to increasing yield, efficiency and labor independence. Such an increasing automation level offers excellent opportunities for Marel to strengthen its position as the industry leader in end-to-end turkey processing solutions.
Prestage Farms chooses Marel's end-to-end turkey solutions
Air chilling makes for a unique greenfield
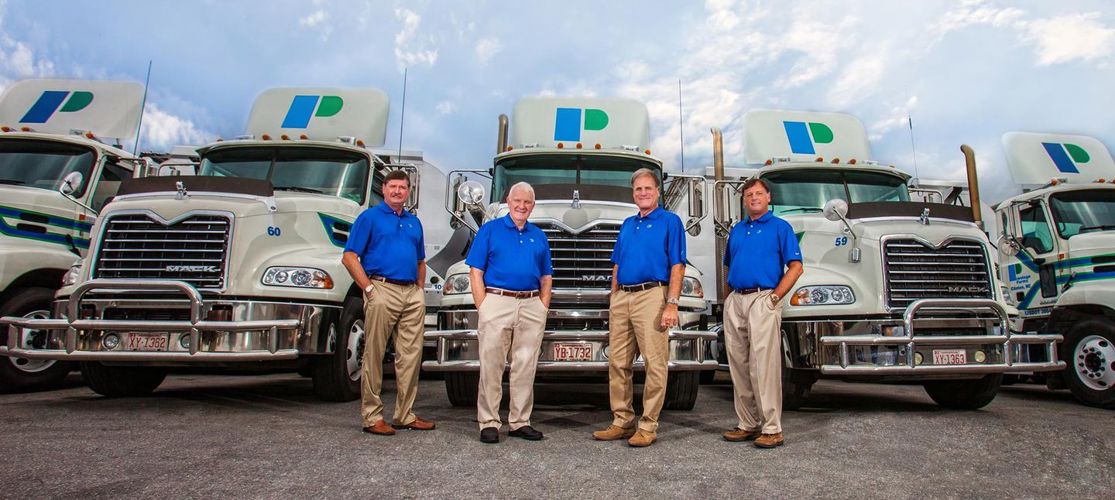
US processor Prestage Farms is cooperating with Marel to build a reference greenfield turkey processing facility in Kershaw County, South Carolina. The new plant is expected to be completed by end of 2022. For Marel, the Prestage Farms greenfield is the largest turkey project ever. Marel Poultry EVP Roger Claessens says, “The Prestage Farms project is a significant step for Marel in our strategy to align our turkey portfolio with the changing markets. Prestage Farms is the culmination of our program becoming the reference in the North American turkey industry.”
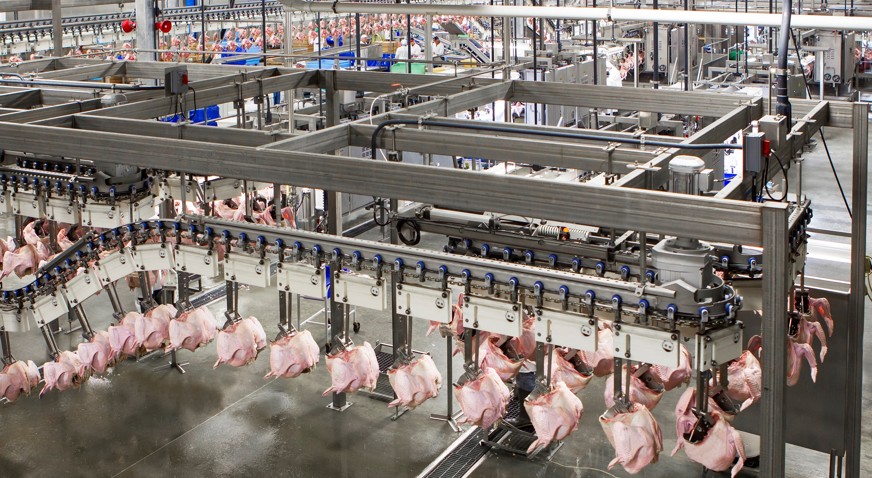
End-to-end solutions
The new Prestage Farms processing plant will feature an end-to-end Marel setup with multiple lines, from defeathering to deboning and inspection, with a total capacity of 6,000 birds per hour. The opening of the new greenfield plant is expected by the end of 2022.
Roger Claessens states, “This continues our journey in the US of providing an increasing number of full-line integrations. Marel is recognized as the supplier who is able to take end-to-end responsibility with regards to quality and efficiency. Prestage Farms chose us as their leading partner for the greenfield turkey processing plant, because Marel is the only party that can meet this demand.”
Quality and efficiency
There are many advantages to the end-to-end approach, allowing turkey processors to make giant leaps forward to quality and efficiency.
- The efficiency in the plant is secured by the seamless logistic flow and the overall knowledge of the processes.
- The turkey processor instantly knows who to address in case of an issue. In which only one partner is There’s only one and the same partner responsible for every piece of equipment and software in the plant.
- The digital connection, makes it possible to connect different data points in the process and act on that, get insights, control machines etc., which would be impossible with a mix of suppliers.
After Lincoln Premium Poultry and Bell & Evans, Prestage Farms is Marel’s third big greenfield project in a short time to illustrate the end-to-end integration trend in the US market.
Focus on automation
Prestage Farms’ new facility, located at the Governor’s Hill Industrial Park in Camden, will process turkey products using state-of-the-art technology and high levels of automation. The facility will utilize technologies that will increase sanitation and the shelf life of products.
The project’s initial focus was on automation. This matched very well with Marel’s turkey evisceration portfolio that has been overhauled step by step over the last years, up to the point of presenting a market-tailored program that really makes a difference. Now, the fully automated evisceration process offers high performance, labor savings and optimal ergonomics.
Besides evisceration, the high level of automation in the processing plant will also be substantially visible in the Marel defeathering line, in the ACM cut-up line and in the FHF deboning line. These automated inline solutions have proven to be at the forefront and best-in-class in the turkey industry.
Air chilling creates a unique package
What defines Prestage Farms as an outstanding project, is the chilling process by air. This largest inline air chilling tunnel for turkeys in the US really differentiates the plant from all previous turkey processing plants. Marel’s in-depth knowledge of turkey air chilling brings more influence on appearance, tenderness, quality, yield, throughput and end-to-end connected product data.
Over the last decade, Marel has made an effort to create the best-in-class turkey processing solutions, with a proven performance in US market. The combination with air chilling forms a unique, distinctive package that made President Dr. Ron Prestage decide to partner with Marel.
End-to-end traceability
The digital layer in the Prestage Farms plant, shaped by an Innova software platform, ensures an end-to-end traceability. From defeathering up to dispatch, product data is gathered to stay with every single product. Thanks to the complete inline configuration, the track and trace functionality covers the entire plant.
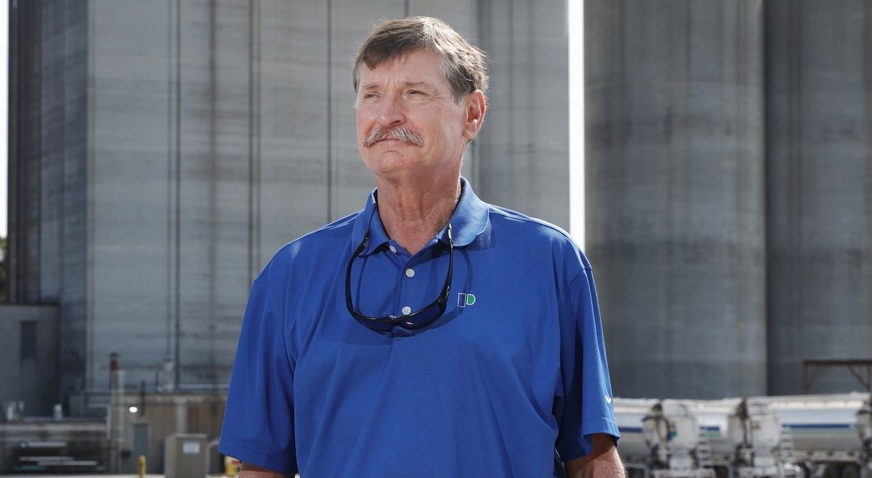
Food safety
Food safety is top priority in the new turkey plant. Prestage Farms applies overarching systems and general plant-wide measures to look after maximum hygiene. Highest attention to food safety is also supported by multiple SensorX X-ray solutions to detect bones and foreign material in turkey fillets.
Shared sustainability
Prestage Farms and Marel share the same vision on sustainability. Prestage Farms is committed to producing wholesome and delicious food in an environmentally responsible way. Marel is always finding ways to make the most efficient use of resources. Maximizing yield is key to decreasing waste in food production, and innovation is a way to get there.
The new Prestage farms processing plant will feature many components that take sustainability into account. First of all, air chilling will lead to a massive reduction of water use, compared to water chilling. The complete automation of the evisceration department will also result in a decrease in water consumption in comparison with a manual process, which is still common in turkey processing. Last but not least, all systems are set to get the right product at the right moment, optimizing the use of raw material and reducing environmental footprint.
Get in touch
Our dedicated team is here to help and answer any questions you may have. Please complete the form, and we’ll get back to you as soon as possible. We look forward to hearing from you.