Marel is the leading global supplier of advanced standalone equipment and integrated systems to the fish industry. Whatever your organization’s size or objectives, we have the products and expertise to help your business thrive and become more sustainable.
The robotic revolution in fish packing is here
Exclusive anniversary promotion on Marel scales
Tougher than the rest
Smarter sushi production
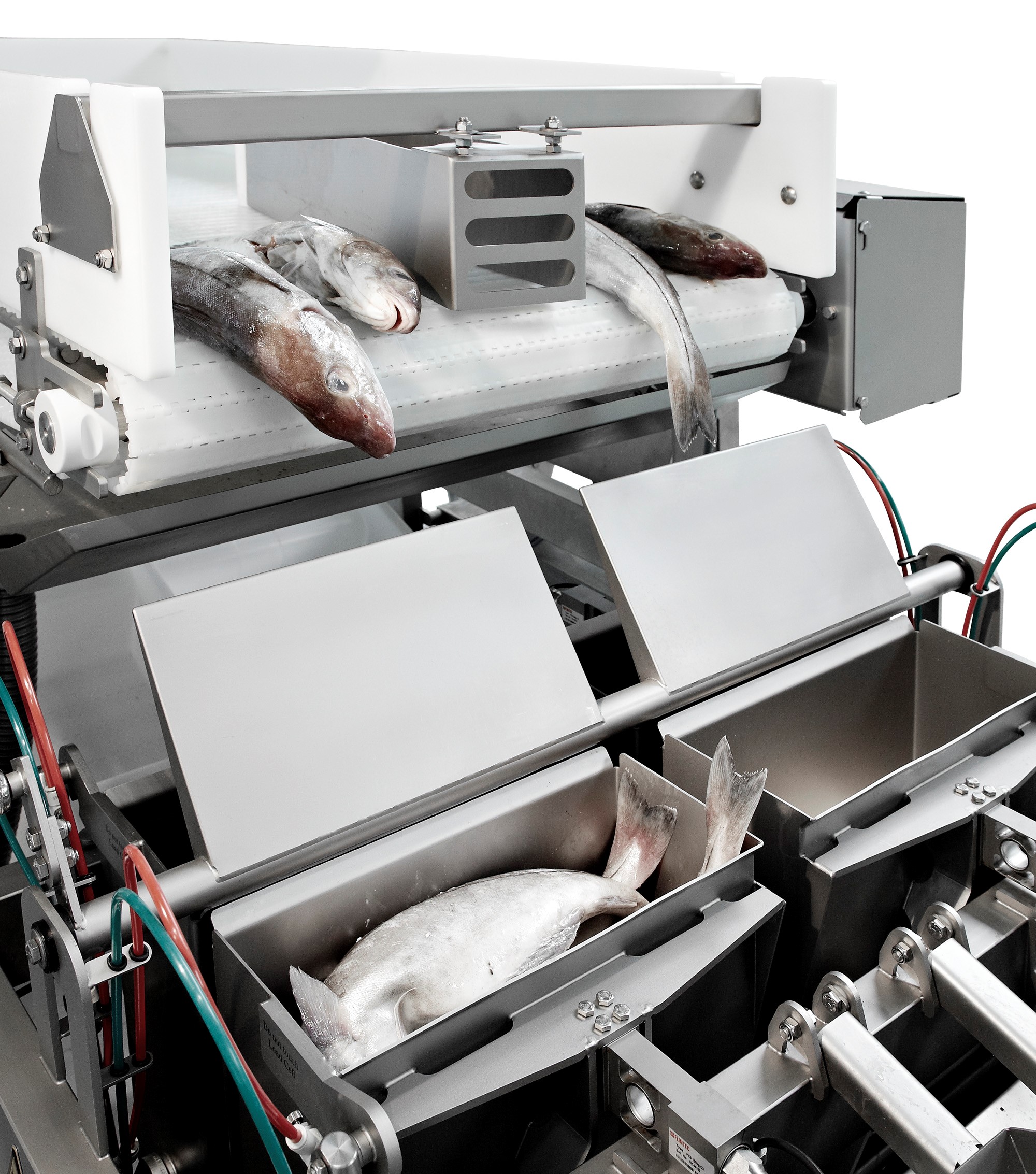
Innovative solutions for fish processing
At the forefront of fish processing
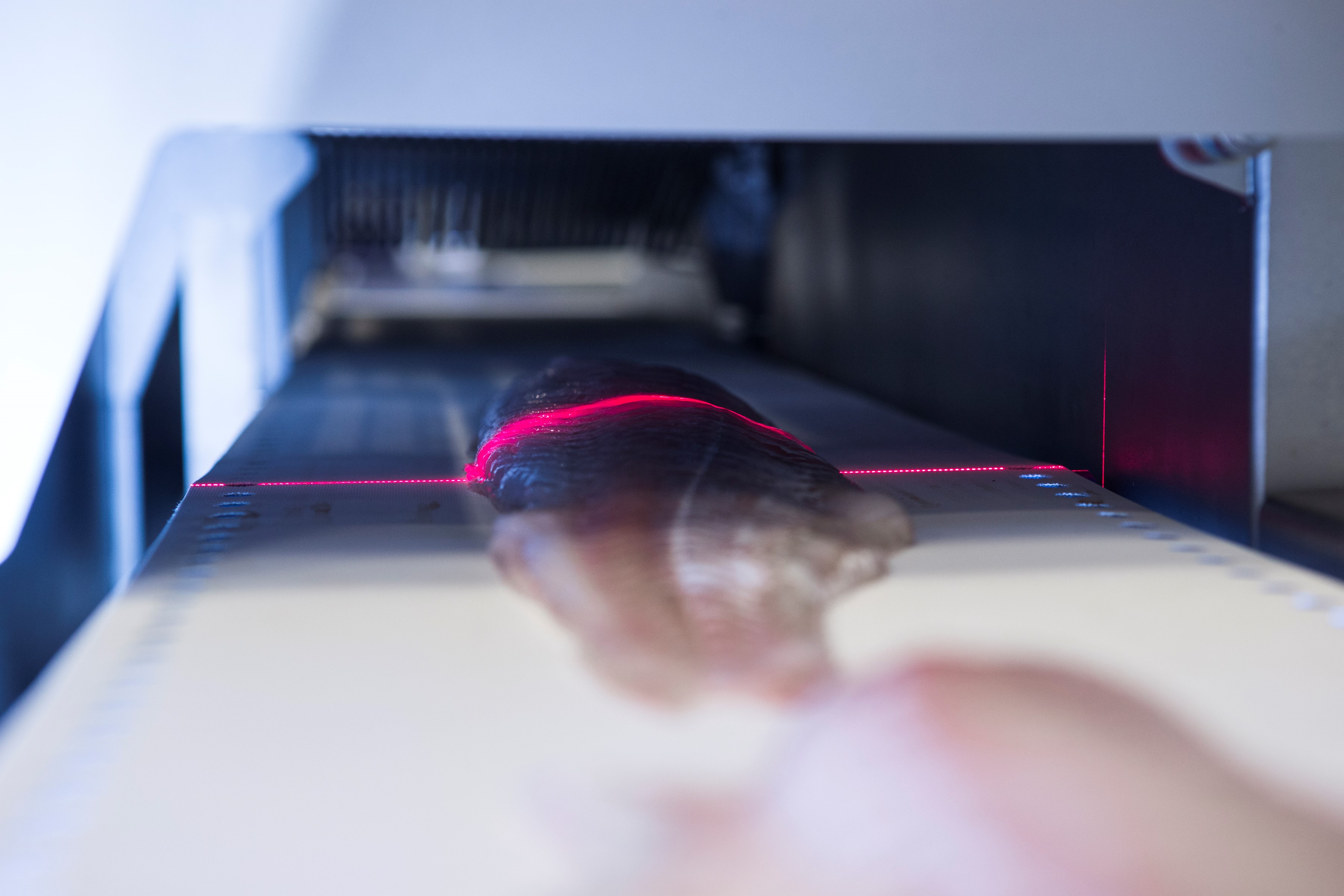
Products and solutions
Marel products and solutions help fish processors optimize yield, quality, throughput and other critical factors across the whole value chain. Ranging from individual units for specific processes such as weighing, cutting and bone removal, to complete solutions such as grading, filleting, portion-cutting and slicing lines, our equipment is built for the harsh fish processing environment, with hygiene and safety always in mind.
Innova Food Processing Software
Innova is a powerful and comprehensive software that collects and collates data, allowing you to improve perfomance and enhance productivity.
Read more about Innova software
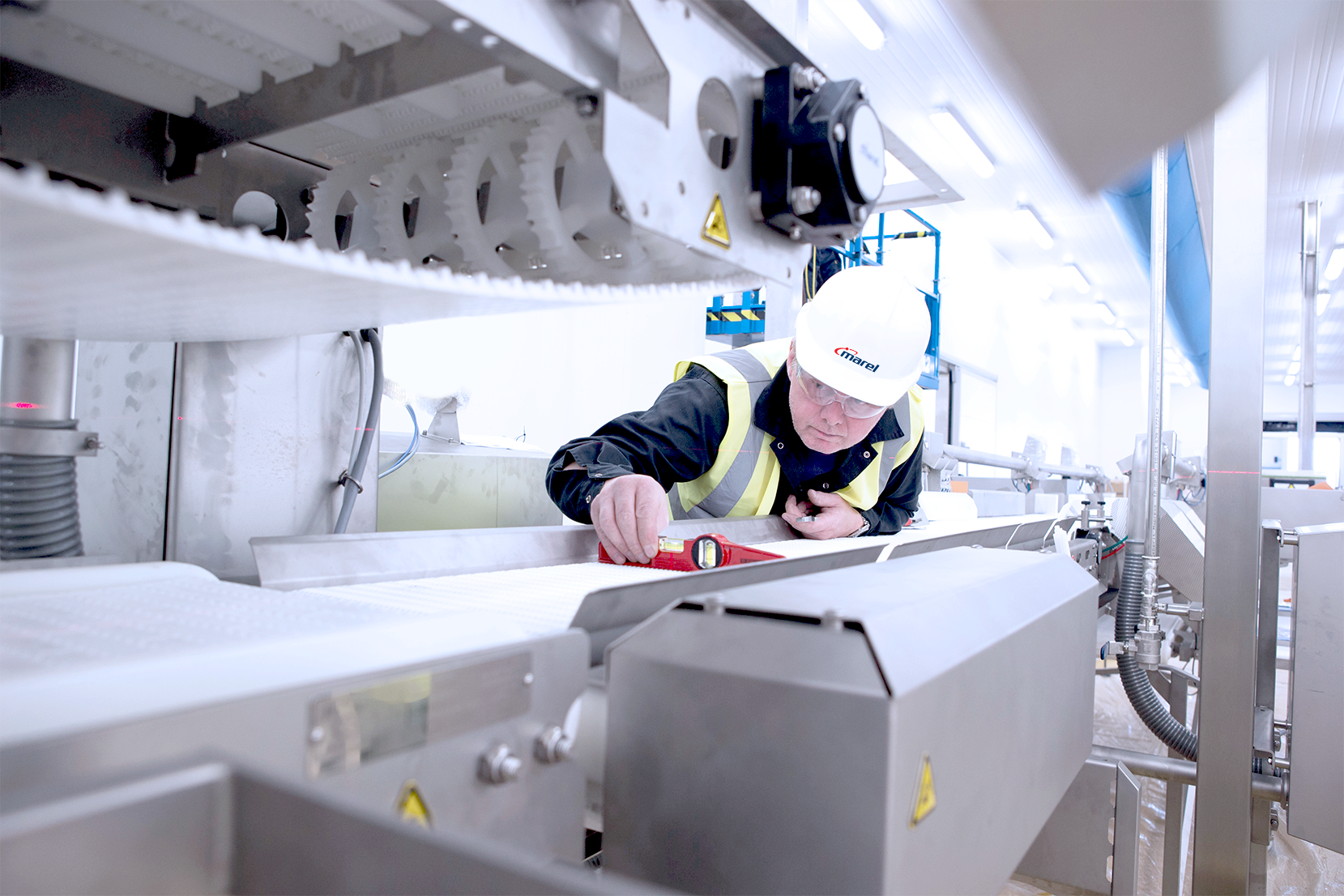
Service
Marel’s service solutions are tailor-made to suit your specific needs. Each solution is tailored to the site and production specifics, to maximize productivity across the production line.
Our global service network takes the worry out of maintenance, making sure your operation remains optimized and competitive. We are always striving to enhance our global reach while never compromising on our local service relationships.
Wherever you are, Marel’s sales and service specialists are close by and ready to help.
Customer stories
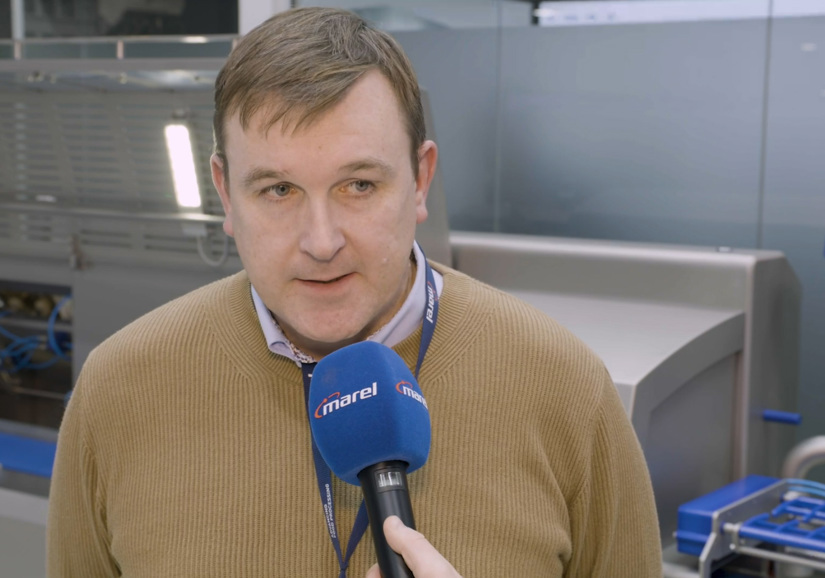
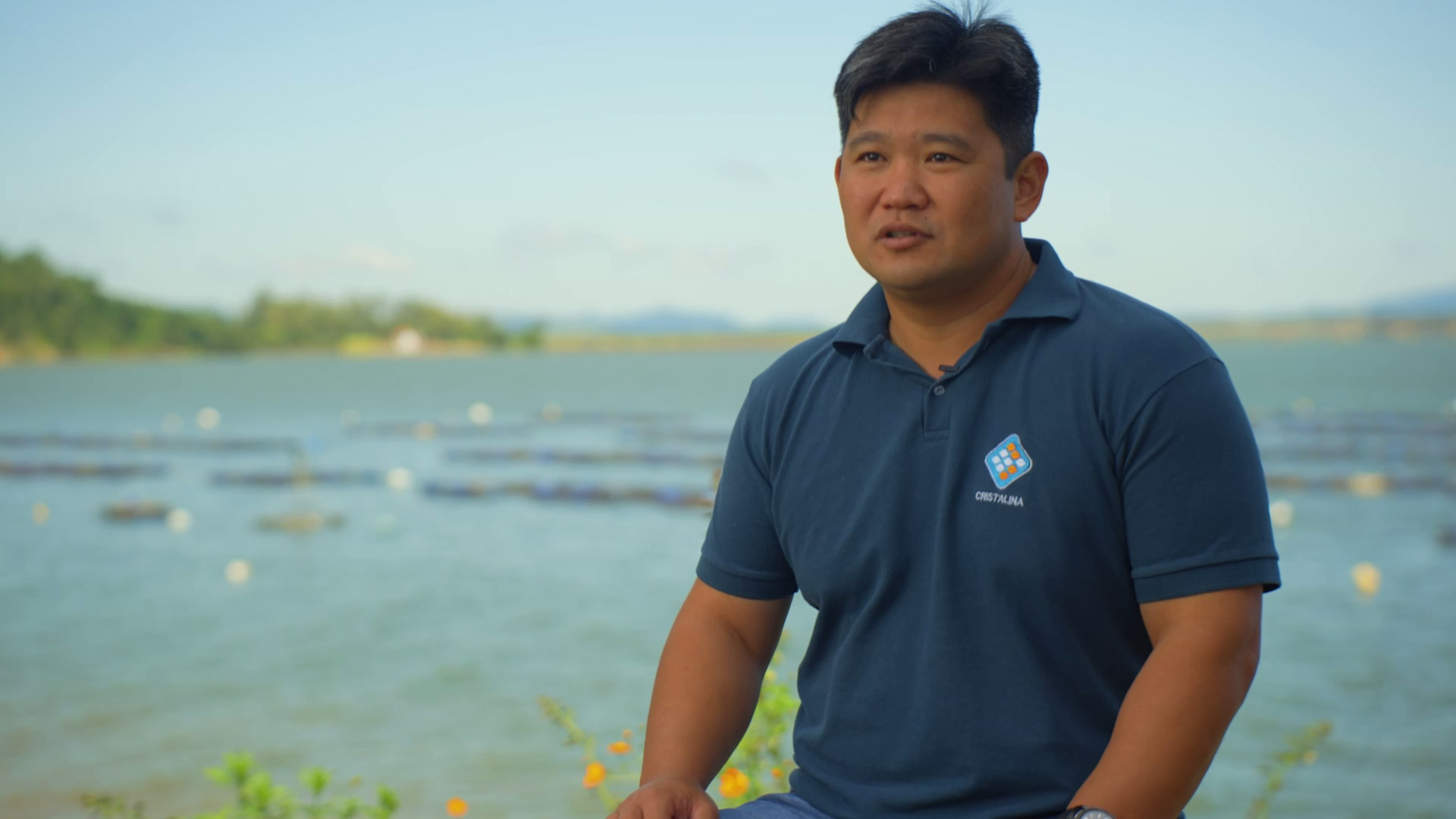
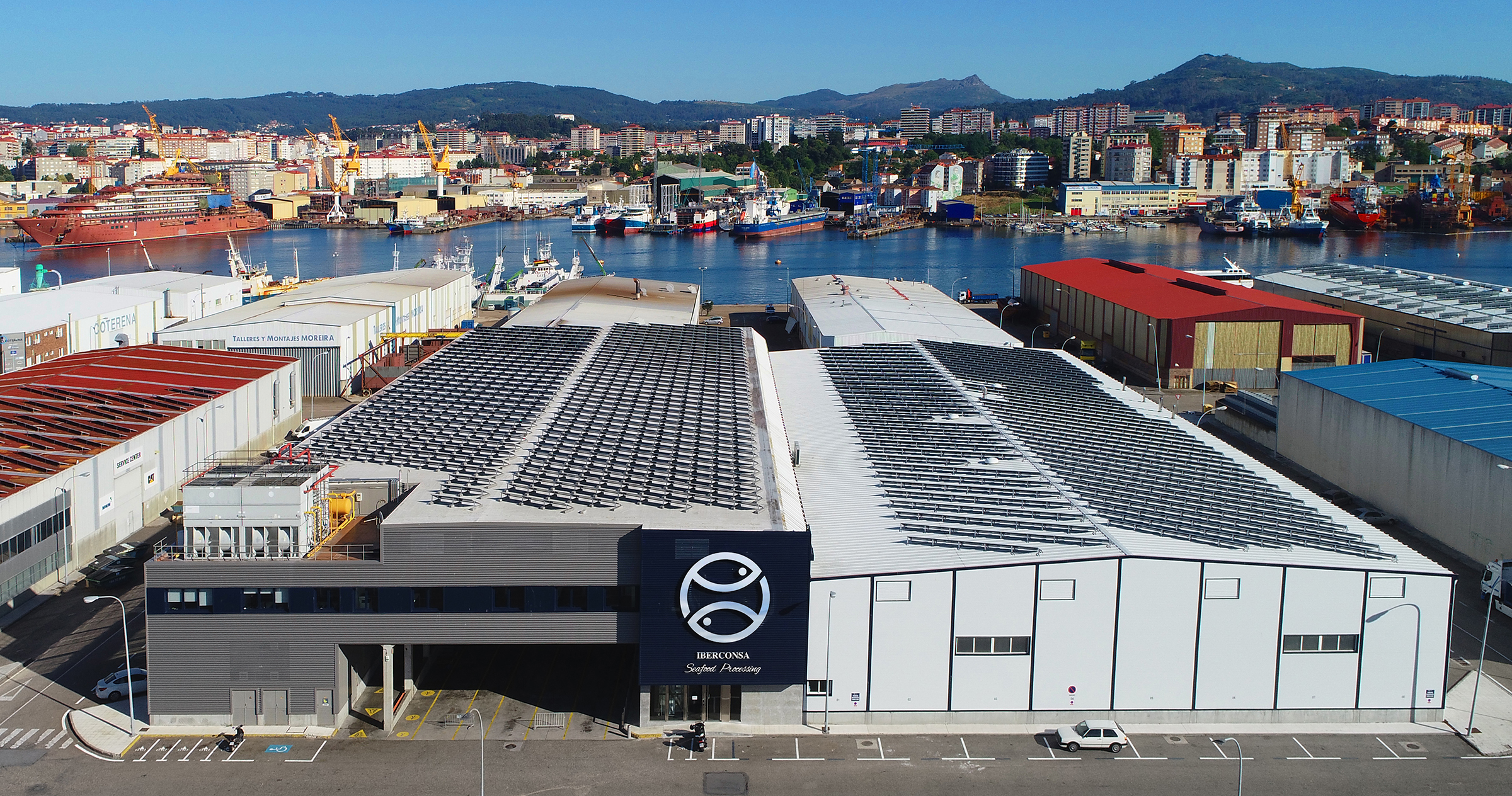
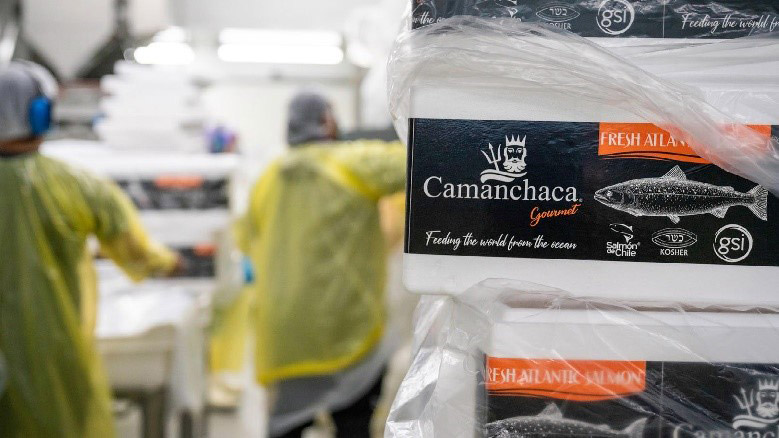
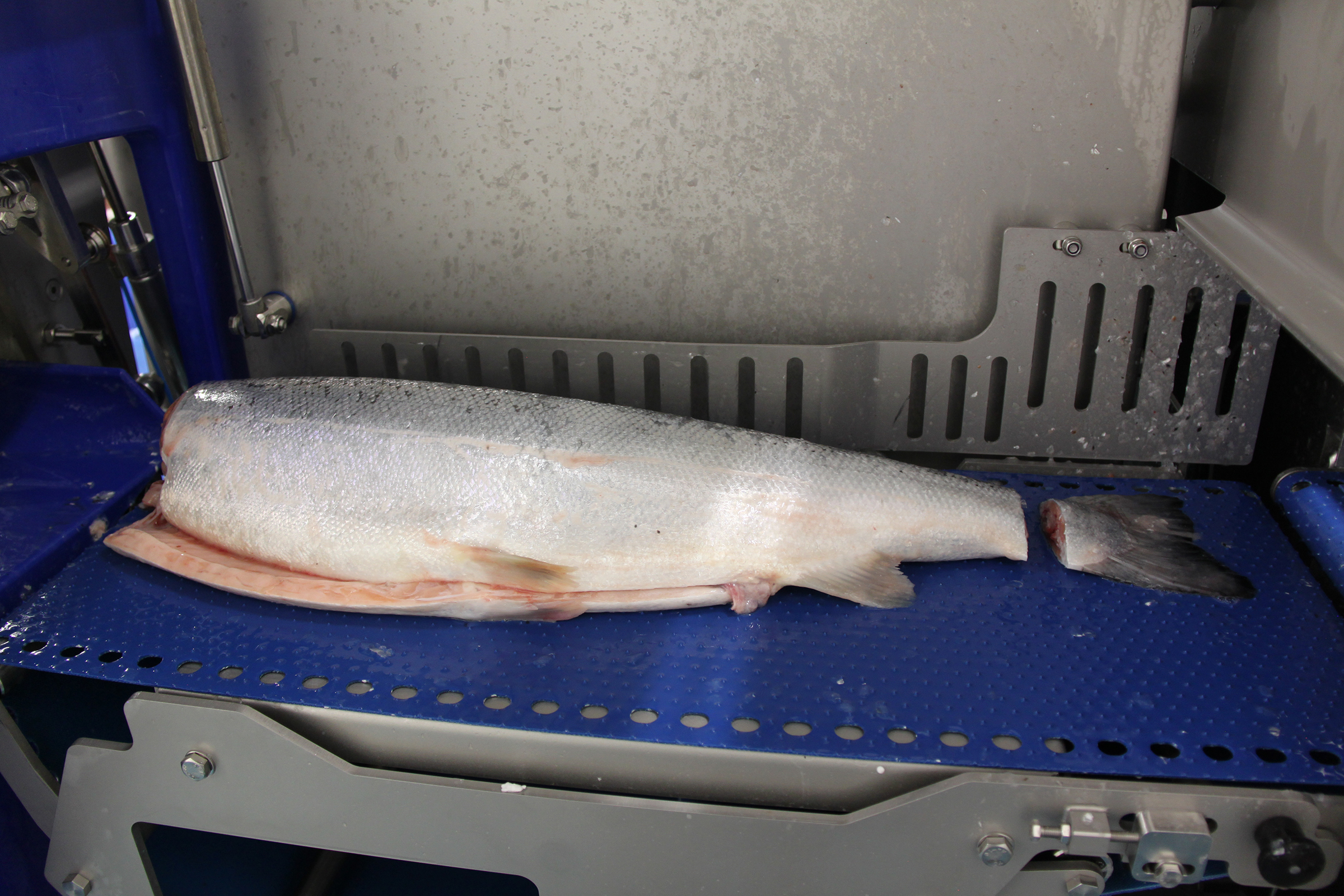
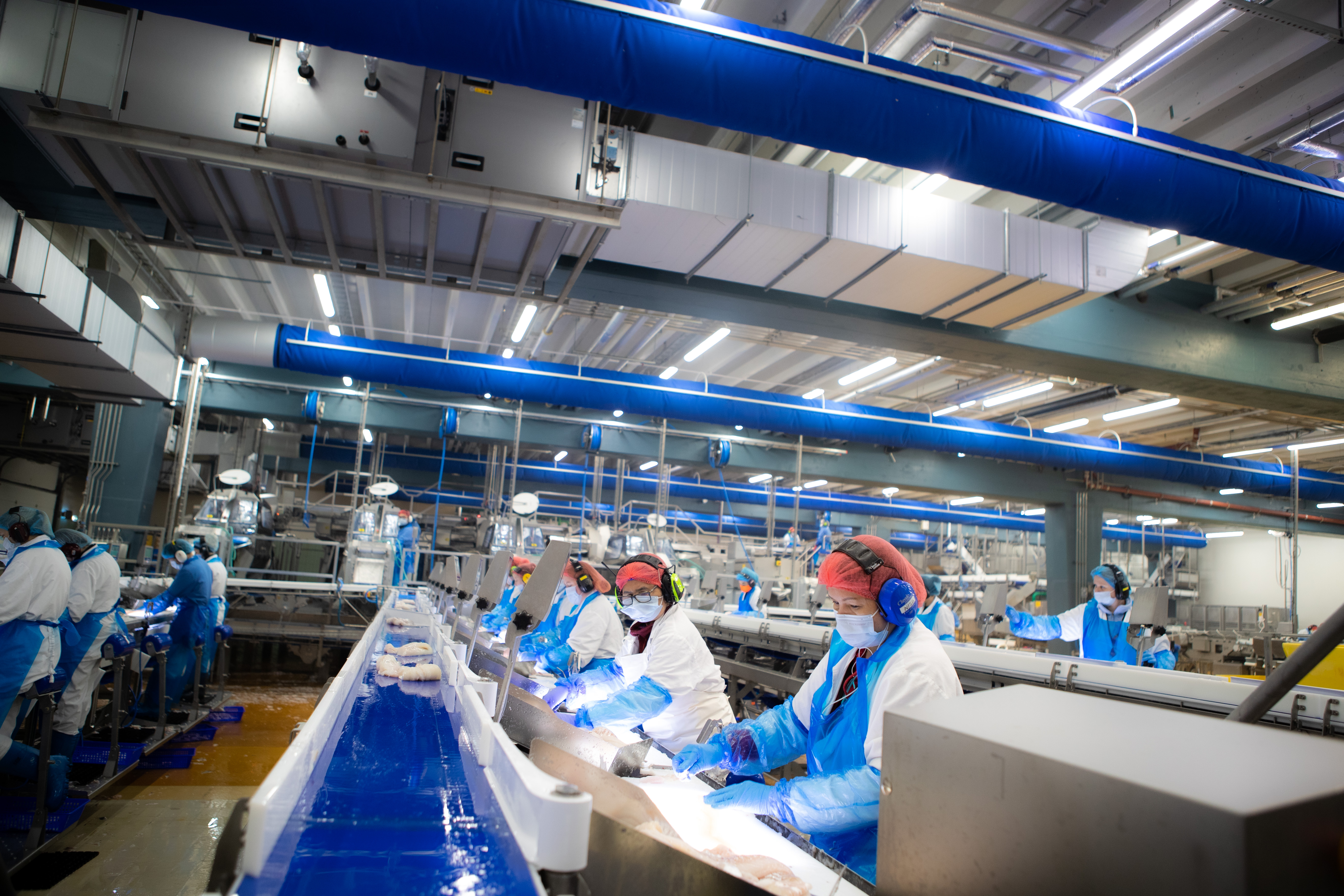
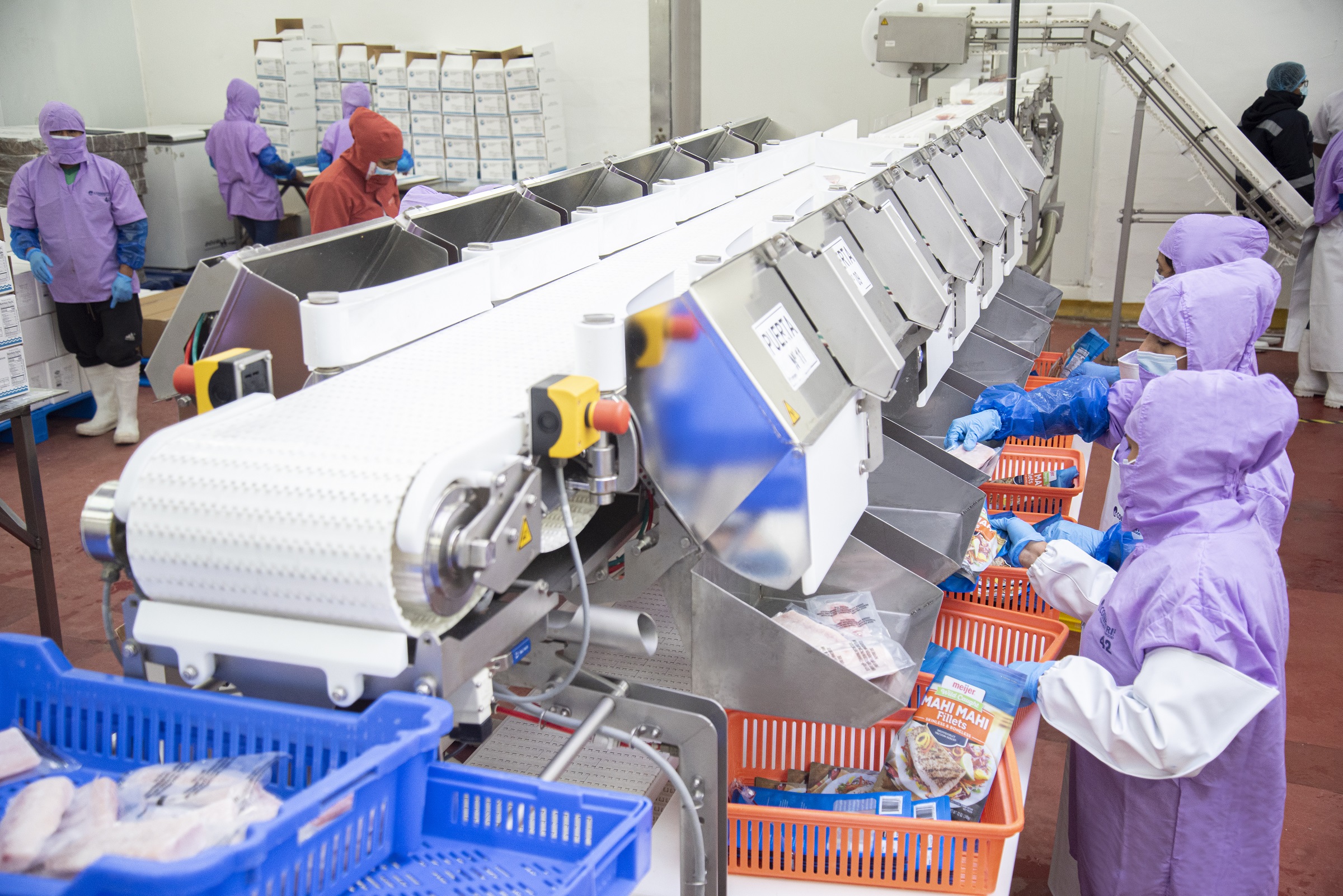
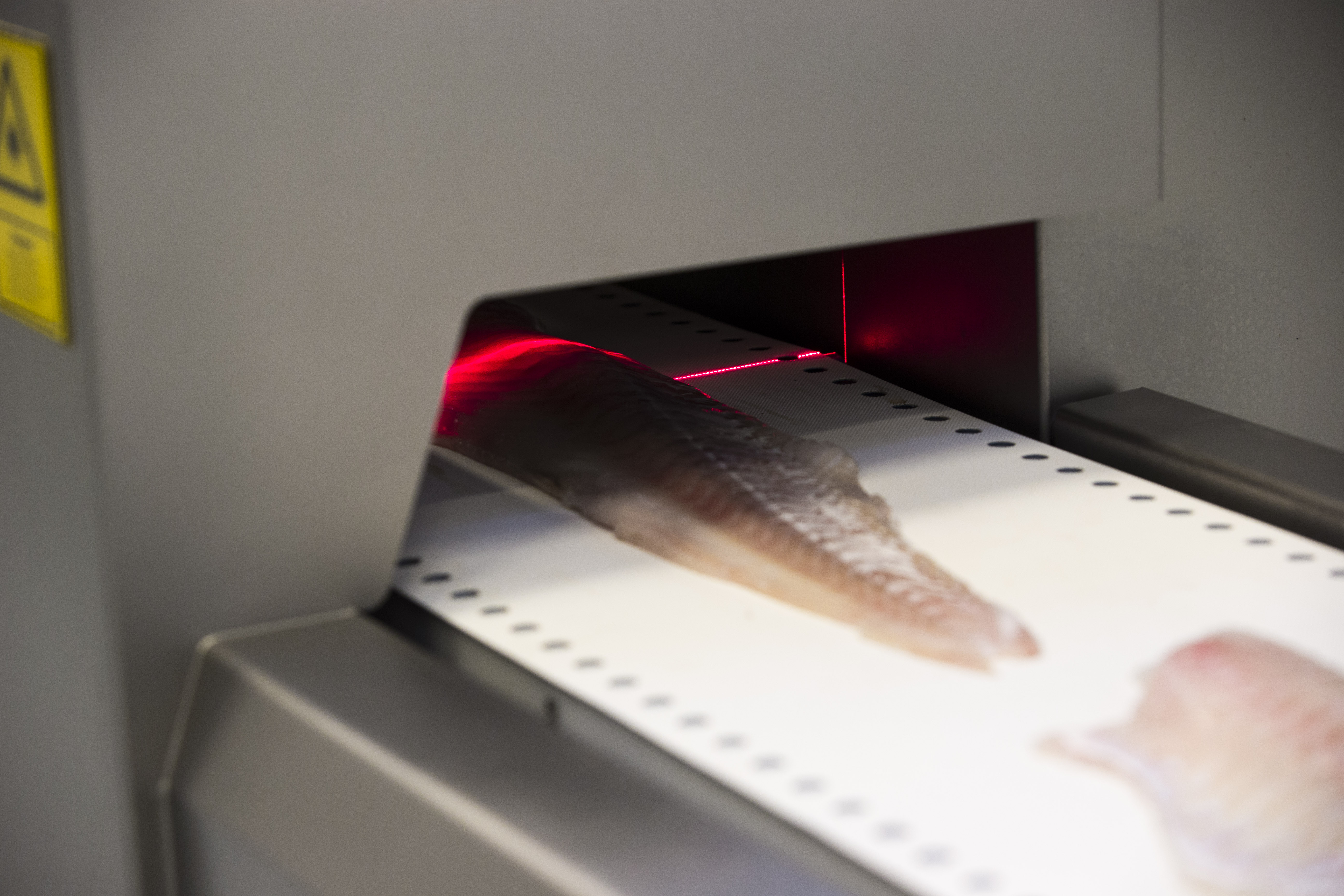
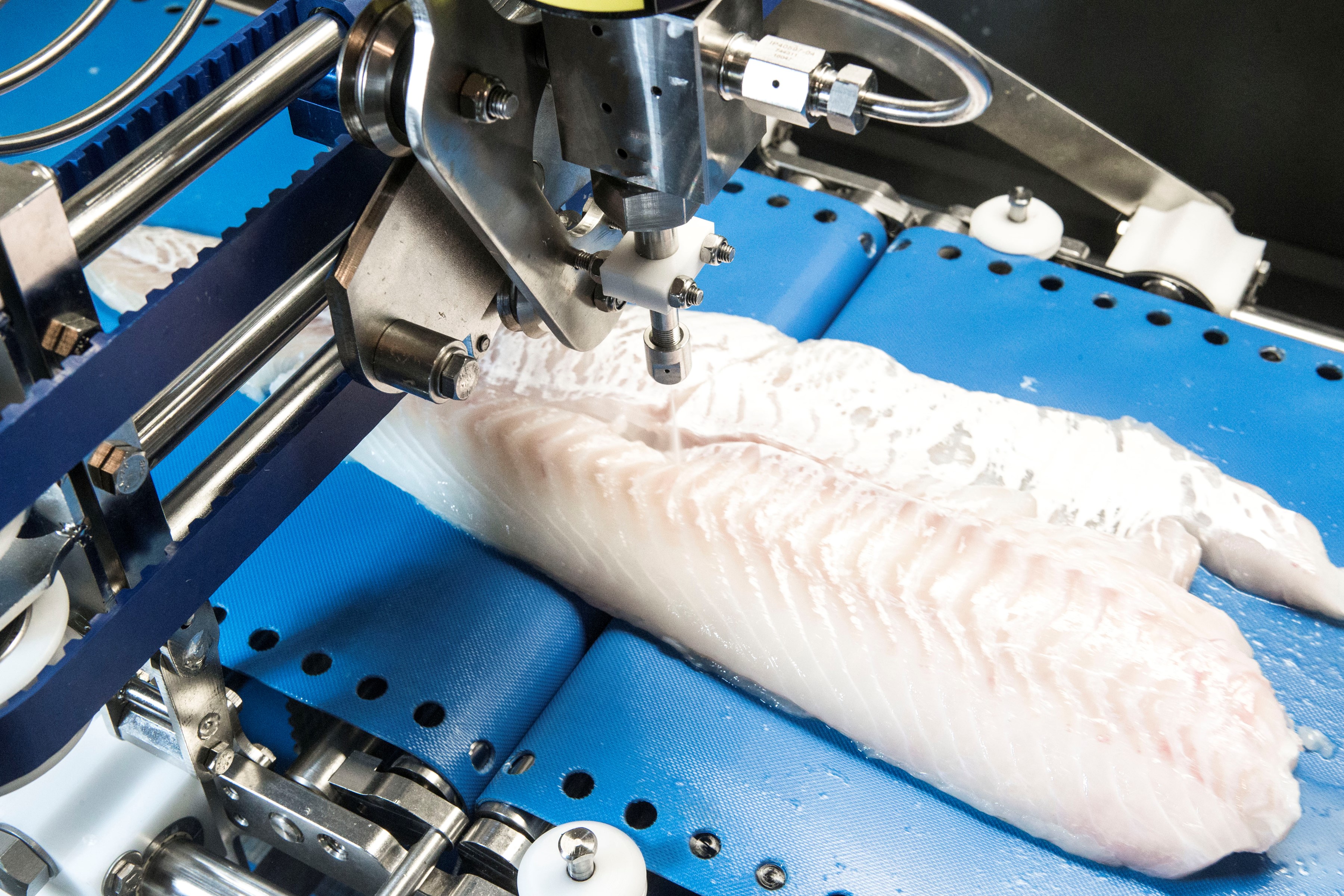
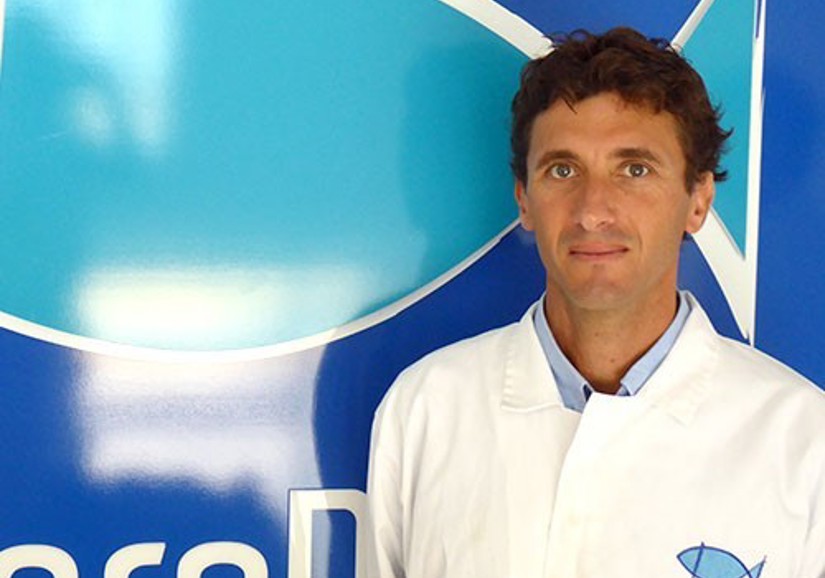