“We started out with 120,000 broilers, expecting to grow to 150,000. This growth became a reality very soon,” says Joop Eskes. After that, some changes have taken place. In 2014, the German PHW Gruppe, known for its Wiesenhof brand, became a co-shareholder of Esbro. Due to a fire at the plant in Bogen, the company had to move ahead faster than expected. So in February of this year, Esbro accelerated to two shifts.
Accelerated expansions at Esbro
Fast changes to two shifts and two complete filleting solutions
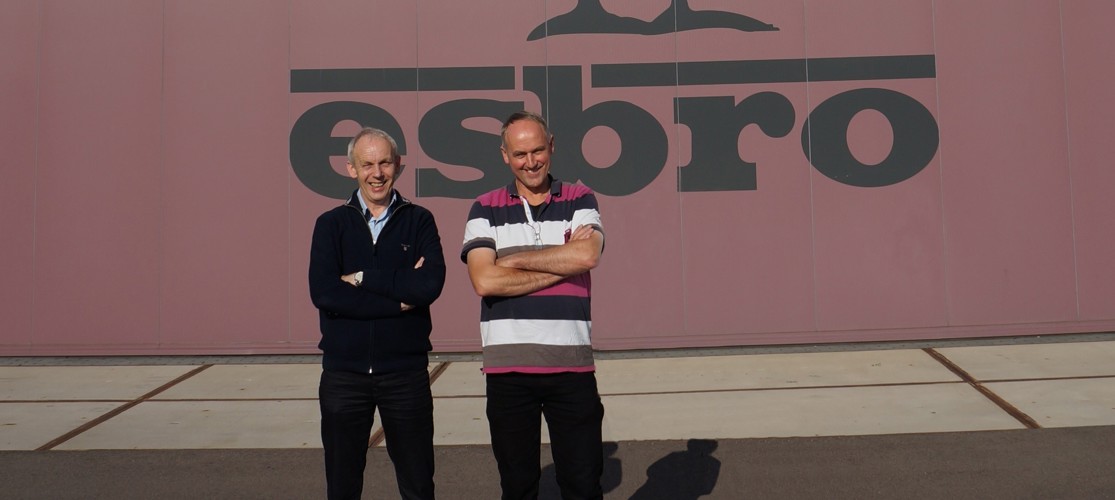
Since its opening in 2013, the newly built Esbro poultry processing plant in Wehl, the Netherlands, has experienced some major developments. Capacities, working hours and end products have all been significantly expanded. Fortunately, general manager Joop Eskes was already an entrepreneur with a vision back in 2013; that’s why he set up the Esbro factory in a way to be prepared for any possible expansion. This proved to be necessary even faster than expected.

Acceleration to two shifts
Joop Eskes: “For our organization, the move to two shifts has had a huge impact, but technically the plant was ready for it. We had space, the capacities and the licenses. Basically, it’s about an improved utilization of the plant with the same systems. But we had to profoundly rethink the structure. By getting the right people in the right places, we managed to achieve a 70% growth in production very short term.”
Two filleting lines
Hardly six weeks after the change to two shifts, the pressure was on to set up two new, complete filleting lines. And so in April 2015 two AMF filleting lines, together with two SensorX and batching/grading solutions were installed. “In spite of the fast installation, the entire process runs fine. The filleting machines have an excellent yield; I’m very satisfied with them,” says Joop Eskes.
Preventive maintenance
Expansion by 140,000 bpd to 235,000 bpd was a huge organizational challenge. The service department of Marel immediately stepped up and supported Esbro in adjusting the schedules. There was not a single moment that the plant was shut down and downtime was negligible.
Joop Eskes attaches great importance to the service program, “We did what Marel recommended: straight away we implemented the preventive maintenance program in the design of the plant. Having this much production time per day, we don’t want to face any downtime. Though such a complete maintenance program may seem quite a big expense, it very much reduces downtime, which is extremely important.”
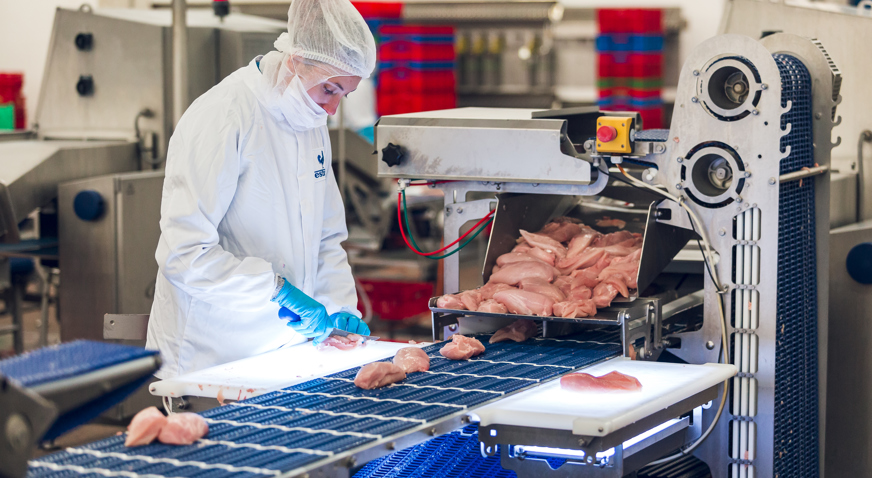
Unique wing cutting
The feed from the cut-up process to the new filleting lines was also changed; two of the three cutting lines were made identical. One of the additions implemented was a JLR leg cutting module for being able to make anatomical legs too.
Together, the Combined Rate Limiting and Floating Weight Control software technologies in the ACM-NT cut-up line ensure a consistent feed and an optimal weight distribution using available products, supplied from the cutting lines. With the help of these technologies, Esbro reserves a reasonably high percentage of the total volume of calibrated wings for QSR restaurants.
These wings are cut in the first cutter; all other wings are processed in the second wing cutter. This is a unique method of processing wings.
Breast caps calibration
All breast caps run over the Marel grading line; a certain number of breast caps per minute of a certain weight range are graded to the filleting lines. If this number can’t be achieved, the bandwidth opens up. When necessary, such adjustments are completely software controlled.
In the two AMF lines both fillet and tenderloin are inspected with the help of a SensorX bone detector so as to meet the highest quality standards for a diverse group of customers. Esbro also has at its disposal a Marel Custom Grader solution for the efficient production of fixed weight packs.
Under the same roof
Joop Eskes: “Looking at the developments in the international poultry market, we can draw only one conclusion: we have to offer more added value under the same roof. We’ve got the space to put up another hall next to the current one. Not so much as to process more broilers, but to process and model our end products.“
Company website: esbro.nl
Get in touch
Our dedicated team is here to help and answer any questions you may have. Please complete the form, and we’ll get back to you as soon as possible. We look forward to hearing from you.